FMEA: Methode, Ablauf und Ziele in der Übersicht für effektives Risikomanagement
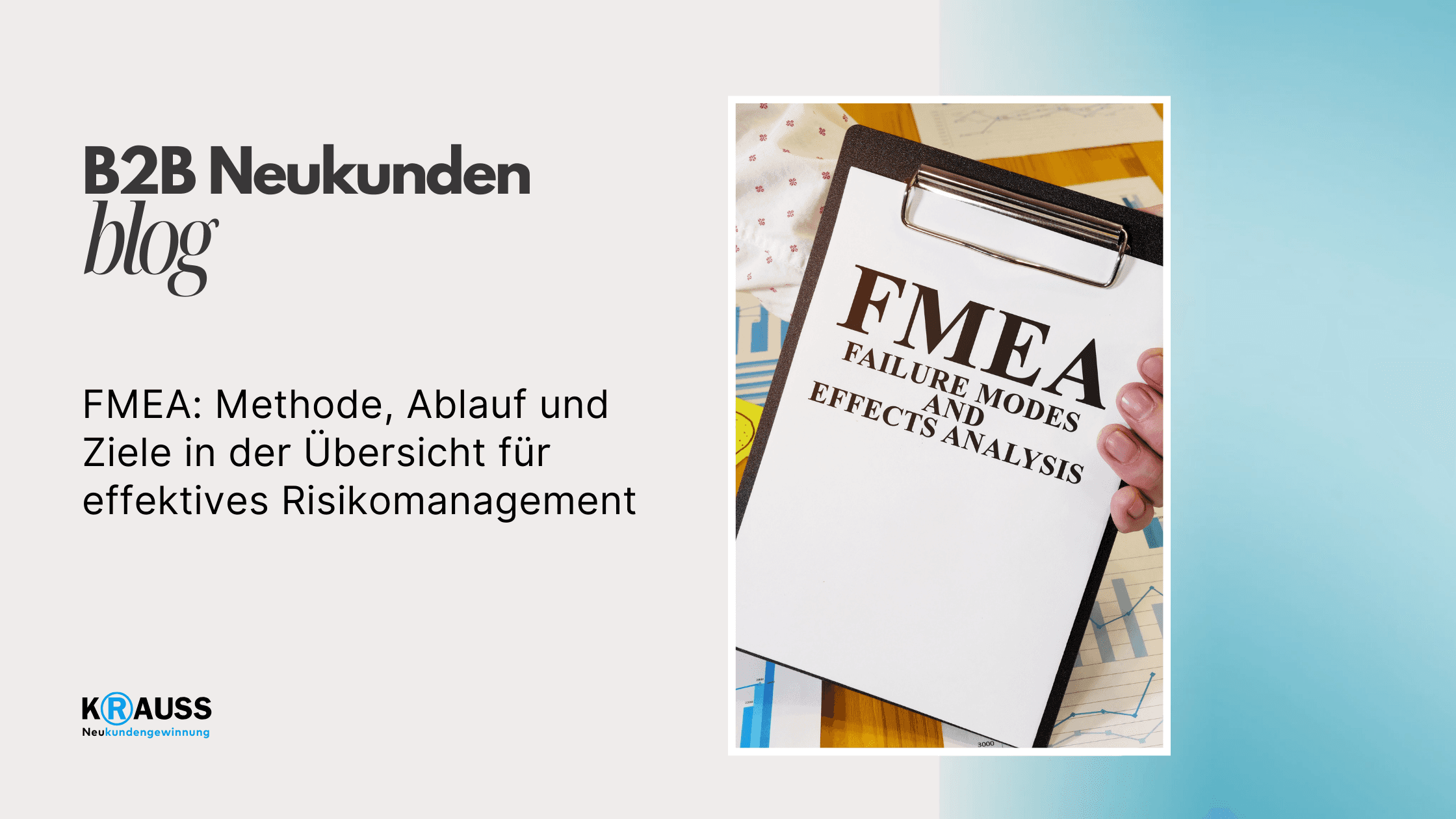
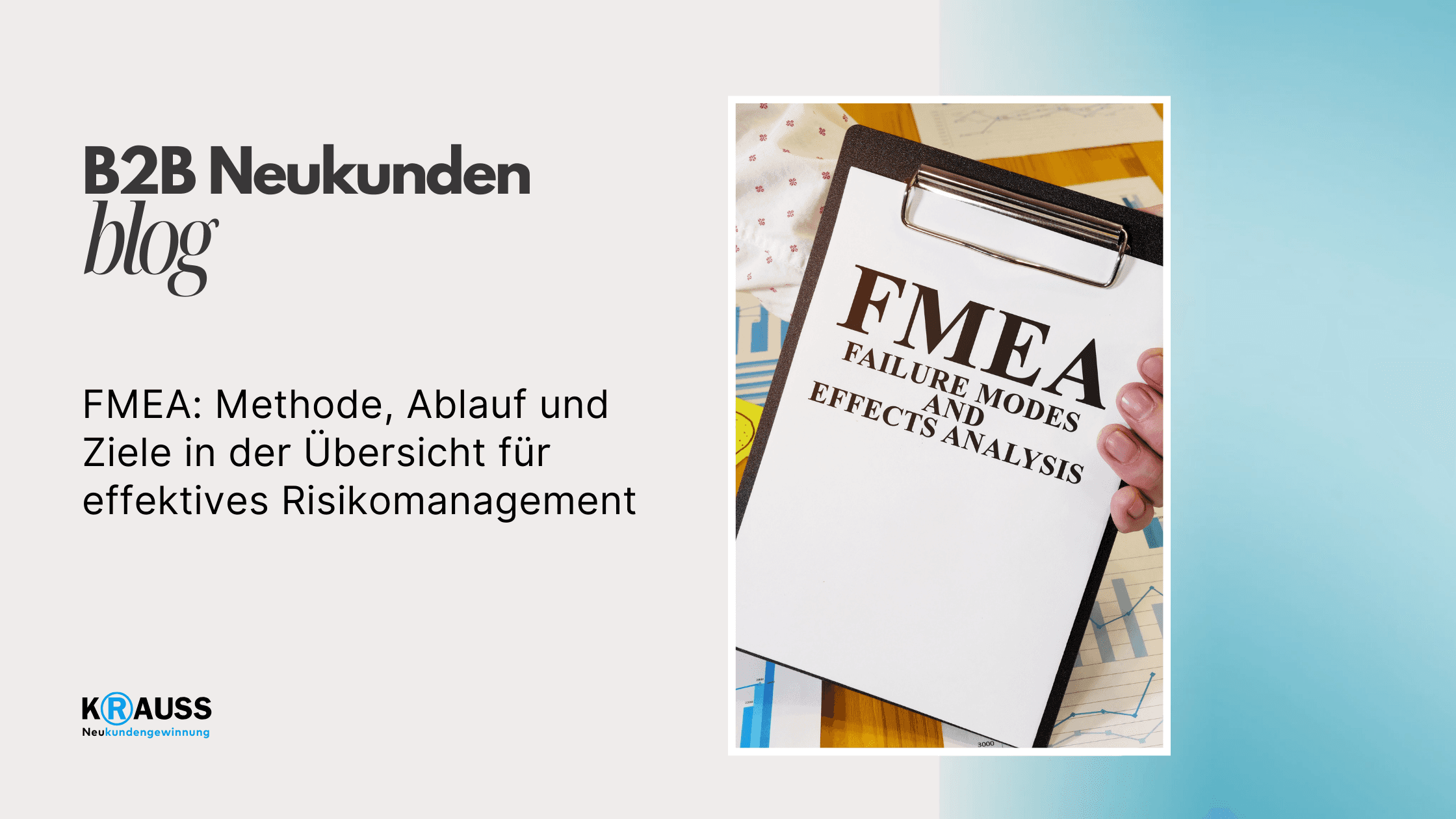
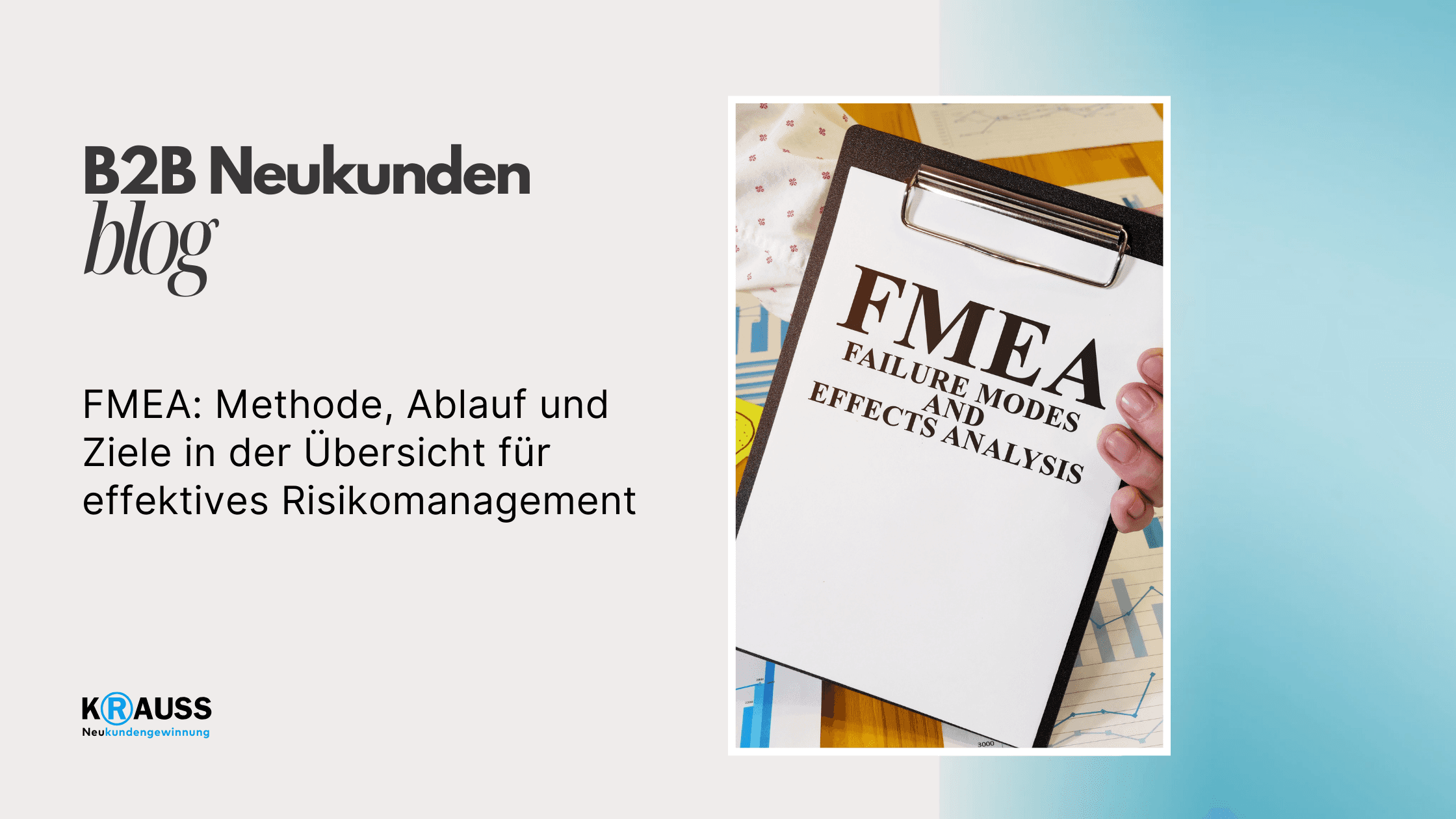

Freitag, 2. August 2024
•
5 Min. Lesezeit
•
FMEA ist eine wichtige Methode zur Risikoanalyse, die Ihnen hilft, potenzielle Fehler in Ihrem Produkt oder Prozess zu erkennen. Durch die Anwendung von FMEA können Sie proaktive Maßnahmen ergreifen, um die Qualität und Sicherheit Ihrer Projekte zu erhöhen. Dies ist entscheidend, um spätere Probleme zu vermeiden und die Zufriedenheit Ihrer Kunden sicherzustellen.
Der FMEA-Prozess umfasst verschiedene Schritte, die systematisch durchgeführt werden, um Unsicherheiten zu identifizieren. Indem Sie diese Methode in Ihr Projektmanagement integrieren, können Sie gemeinsam mit einem Team wertvolle Erkenntnisse gewinnen, die die Effizienz und Effektivität Ihrer Entwicklungen steigern. Die richtige Anwendung von FMEA führt zu einer besseren Planung und einem klareren Überblick über mögliche Risiken.
Wenn Sie mehr über diese Methode und die spezifischen Abläufe erfahren möchten, sind Sie hier genau richtig. Der folgende Artikel wird Ihnen alle wichtigen Informationen und praktischen Tipps zur FMEA bieten, damit Sie die Vorteile dieser Methode optimal nutzen können.
Key Takeaways
FMEA hilft Ihnen, potenzielle Fehler frühzeitig zu identifizieren.
Ein strukturierter Prozess ist entscheidend für den Erfolg der FMEA.
Der Einsatz von FMEA steigert die Qualität und Sicherheit Ihrer Produkte.
Grundlagen der FMEA
In diesem Abschnitt wird die FMEA erklärt, einschließlich ihrer Definition, Bedeutung und ihrer historischen Entwicklung. Dies hilft Ihnen, ein besseres Verständnis für die Methode und ihre Anwendung in der Risikoanalyse zu entwickeln.
Definition und Bedeutung
Die Fehler-Möglichkeiten- und Fehler-Einfluss-Analyse (FMEA) ist eine systematische Methode zur Identifizierung und Bewertung potenzieller Fehler in einem Produkt oder Prozess. Ziel ist es, Risiken frühzeitig zu erkennen und geeignete Maßnahmen zur Vermeidung oder Minderung dieser Risiken zu ergreifen.
Die FMEA spielt eine wichtige Rolle in der Qualitätssicherung, da sie Ihnen hilft, die Sicherheit und Qualität Ihrer Produkte zu gewährleisten. Durch die frühzeitige Erkennung von Problemen können Sie kostspielige Fehler und negative Auswirkungen auf die Kundenzufriedenheit reduzieren. Ein interdisziplinäres Team führt die FMEA durch, um verschiedene Perspektiven und Fachkenntnisse in die Risikobewertung einzubeziehen.
Historie und Entwicklung der FMEA
Die FMEA-Methode wurde in den 1960er Jahren von der US-Armee zur Verbesserung der Sicherheit in militärischen Projekten entwickelt. Später wurde die Methode in der Automobilindustrie adaptiert, um die Qualität und Zuverlässigkeit von Fahrzeugen zu erhöhen.
Im Laufe der Zeit hat sich die FMEA weiterentwickelt und ist heute in vielen Branchen ein wichtiges Werkzeug für die Risikoanalyse. Sie wird häufig in der Produktentwicklung, im Maschinenbau und im Gesundheitswesen eingesetzt. Die Methode hilft Ihnen, proaktiv mit potenziellen Risiken umzugehen und Prozesse effizienter zu gestalten, was zu einer höheren Produkt- und Prozessqualität führt.
Arten der FMEA
Die Analyse der Fehlermöglichkeiten und deren Auswirkungen erfolgt in verschiedenen Arten, jede mit einem speziellen Fokus. Hier werden die Design-FMEA, Prozess-FMEA und System-FMEA betrachtet, um zu zeigen, wie sie in unterschiedlichen Kontexten angewendet werden.
Design-FMEA
Die Design-FMEA konzentriert sich auf die Entwicklung von Produkten. Ihr Ziel ist es, potenzielle Fehler in der Produktgestaltung zu identifizieren, bevor diese in die Produktion gehen. Dabei werden verschiedene Aspekte wie Materialien, Funktionen und Entwurf analysiert.
Wichtige Schritte in der Design-FMEA sind:
Identifikation von Fehlerarten: Was könnte bei Ihrem Design schiefgehen?
Bewertung der Auswirkungen: Wie wirkten sich diese Fehler auf das Produkt aus?
Risikoprioritätsnummer (RPN): Berechnung der Schwere, Auftretenswahrscheinlichkeit und Entdeckungswahrscheinlichkeit, um Risiken zu priorisieren.
Die Analyse hilft, die Qualität des Endprodukts zu sichern und teure Korrekturen in späteren Phasen zu vermeiden.
Prozess-FMEA
Die Prozess-FMEA befasst sich mit bestehenden Produktionsprozessen. Sie hilft, potenzielle Fehlerquellen innerhalb dieser Prozesse zu erkennen und die Qualität sowie Effizienz zu erhöhen. Anwendungsbeispiele sind Montage-, Fertigungs- und Prüfprozesse.
Wichtige Schritte in der Prozess-FMEA sind:
Prozessflussdiagramm: Erstellen eines Diagramms, um die einzelnen Schritte des Prozesses zu visualisieren.
Fehleranalyse: Untersuchung, bei welchen Schritten Fehler auftreten können.
Massnahmen zur Fehlervermeidung: Entwicklung von Strategien zur Minimierung identifizierter Risiken.
Mit der Prozess-FMEA verbessern Sie die Zuverlässigkeit und Sicherheit Ihrer Abläufe.
System-FMEA
Die System-FMEA wird auf Systeme angewendet, die mehrere Komponenten oder Prozesse beinhalten. Diese Methode betrachtet, wie verschiedene Teile eines Systems zusammenarbeiten und wo Fehler auftreten können.
Wichtige Aspekte der System-FMEA sind:
Systemanalyse: Verständnis der Interaktionen zwischen verschiedenen Komponenten.
Risikoabschätzung: Identifizierung der Risiken, die sich aus diesen Wechselwirkungen ergeben.
Systemintegration: Sicherstellen, dass die einzelnen Bestandteile harmonisch zusammenarbeiten.
Durch die Anwendung der System-FMEA können Sie die Gesamtzuverlässigkeit Ihres Systems steigern und das Risiko von Fehlern verringern.
FMEA-Prozess und Team
Im FMEA-Prozess spielt das Team eine entscheidende Rolle. Es besteht aus verschiedenen Mitgliedern, die unterschiedliche Perspektiven und Fachkenntnisse einbringen. Eine klare Zusammenarbeit ist erforderlich, um potenzielle Fehler und Risiken effektiv zu erkennen und zu analysieren.
Aufbau des FMEA-Teams
Ein FMEA-Team besteht in der Regel aus Fachexperten, die verschiedene Aspekte eines Produkts oder Prozesses vertreten. Dazu gehören Ingenieure, Qualitätsmanager und Produkthersteller. Der FMEA-Moderator ist ebenfalls ein wichtiger Teil des Teams. Er leitet die Diskussion, sorgt für Struktur und stellt sicher, dass alle Stimmen gehört werden.
Die Teammitglieder sollten regelmäßig in Meetings zusammenkommen, um den Fortschritt zu überprüfen und neue Erkenntnisse zu diskutieren. Diese Meetings fördern den Austausch von Ideen und stärken die Zusammenarbeit. Ein gut strukturiertes Team maximiert die Effizienz und Qualität der Fehleranalyse.
Rollen und Verantwortlichkeiten
Innerhalb des Teams hat jedes Mitglied eine spezifische Rolle. Der Moderator ist für die Gesamtdurchführung verantwortlich und hält die Gruppe auf Kurs. Ingenieure analysieren technische Risiken, während Qualitätsmanager sicherstellen, dass Standards eingehalten werden.
Jedes Teammitglied sollte klar definierte Aufgaben haben. Dies könnte Folgendes umfassen:
Datenanalyse: Sammlung und Auswertung relevanter Informationen.
Fehleridentifikation: Erkennen potenzieller Fehlerquellen.
Maßnahmenplanung: Entwicklung von Strategien zur Fehlervermeidung.
Die klare Zuweisung von Rollen fördert die Verantwortung und reduziert Missverständnisse im Team. Ein effektives FMEA-Team arbeitet eng zusammen, um alle Aspekte der Analyse abzudecken und die Qualität stetig zu verbessern.
FMEA-Ablauf
Der Ablauf einer Fehlermöglichkeits- und Einflussanalyse (FMEA) ist ein systematischer Prozess. Er umfasst wichtige Schritte und Methoden, um mögliche Fehler frühzeitig zu erkennen und Risiken zu bewerten. Dies führt zu einer besseren Kontrolle und Optimierung der Produkte und Prozesse.
Strukturanalyse
In der Strukturanalyse erfassen Sie das Produkt oder den Prozess in seiner Gesamtheit. Hierbei erstellen Sie eine Dokumentation der Struktur, die alle Komponenten und deren Beziehungen umfasst. Dies wird oft in Form von Diagrammen oder Tabellen durchgeführt.
Die Analyse hilft Ihnen, alle relevanten Teile zu identifizieren und zu verstehen. Zudem definieren Sie die Funktionen der einzelnen Komponenten. Indem Sie Schwächen in der Struktur identifizieren, können Sie gezielte Änderungen vornehmen, um die Robustheit zu erhöhen.
Funktionsanalyse
Die Funktionsanalyse folgt der Strukturanalyse und fokussiert sich auf die spezifischen Funktionen der identifizierten Komponenten. Hier prüfen Sie, ob jede Komponente ihre Aufgabe erfüllt. Sie analysieren, welche Funktionen kritisch sind und welche möglicherweise versagen können.
In dieser Phase ist es wichtig, auch die Risikoprioritätszahl (RPZ) zu bestimmen. Diese Zahl hilft Ihnen, die Wichtigkeit der jeweiligen Funktion zu bewerten. Bedenken Sie, dass eine klare Funktionsdefinition die Grundlage für die nachfolgenden Schritte der FMEA bildet.
Fehleranalyse
Die Fehleranalyse ist der letzte Schritt im FMEA-Ablauf. Hier identifizieren Sie potenzielle Fehler, die in den vorherigen Analysen aufgetreten sind. Sie bewerten die Wahrscheinlichkeit und die Auswirkungen jedes Fehlers auf das Gesamtsystem.
Jeder Fehler wird dokumentiert und hinsichtlich seiner Schwere und Häufigkeit bewertet. Durch diesen Prozess erfahren Sie, welche Fehlerkorrekturen dringend notwendig sind. Dies ermöglicht ein effektives Risikomanagement und unterstützt die Optimierung Ihres Produkts oder Prozesses.
Bewertung und Management von Risiken
Um die Qualität Ihres Produkts zu sichern und Risiken zu minimieren, ist ein systematischer Ansatz zur Risikobewertung und -management notwendig. Dieser umfasst die Risikobewertung mithilfe der Risikoprioritätszahl (RPZ) und die Umsetzung geeigneter Maßnahmen zur Risikominimierung.
Risikobewertung mit der RPZ
Die Risikoprioritätszahl (RPZ) ist ein wichtiges Werkzeug zur Bewertung von Risiken. Diese Zahl hilft Ihnen, potenzielle Fehler und deren Auswirkungen zu quantifizieren.
Die RPZ wird durch folgende Formel berechnet:
RPZ = Auftretenswahrscheinlichkeit x Schwere der Auswirkung x Entdeckungswahrscheinlichkeit
Auftretenswahrscheinlichkeit: Wie häufig der Fehler auftreten könnte.
Schwere der Auswirkung: Welche Folgen der Fehler hat.
Entdeckungswahrscheinlichkeit: Wie leicht der Fehler erkannt wird.
Mit dieser Methode können Sie Risiken priorisieren. Eine höhere RPZ zeigt an, dass ein Fehler dringender behandelt werden muss. So sichern Sie die Produktqualität und steigern die Kundenzufriedenheit.
Maßnahmen zur Risikominimierung
Nachdem Sie die Risiken bewertet haben, ist es wichtig, gezielte Maßnahmen zur Risikominderung zu ergreifen. Diese Maßnahmen sollten sich auf die wichtigsten Fehlerquellen konzentrieren.
Einige häufige Strategien sind:
Fehlervermeidung: Anpassen von Prozessen, um Fehler schon im Vorfeld zu verhindern.
Schulung: Mitarbeitende in der Fehlervermeidung trainieren.
Qualitätsmanagement: Regelmäßige Überprüfungen und Audits durchführen.
Mit diesen Maßnahmen reduzieren Sie Kosten, die durch fehlerhafte Produkte entstehen können. Gleichzeitig verbessern Sie die Produktqualität und erhöhen die Zufriedenheit Ihrer Kunden.
Häufig gestellte Fragen
In diesem Abschnitt werden häufige Fragen zur FMEA beantwortet. Es wird erklärt, was FMEA ist, welche Schritte sie umfasst und wer daran beteiligt ist. Auch die verschiedenen Arten von FMEA und ihre Dokumentation werden behandelt.
Was versteht man unter einer FMEA und welche Ziele werden damit verfolgt?
FMEA steht für Fehlermöglichkeiten- und -einflussanalyse. Mit dieser Methode identifizierst du potenzielle Fehler und deren Auswirkungen in einem Produkt oder Prozess. Die Ziele sind, die Sicherheit zu erhöhen und die Qualität zu gewährleisten, indem Probleme frühzeitig erkannt werden.
Welche Schritte umfasst der Ablauf einer FMEA-Analyse?
Die FMEA-Analyse erfolgt in mehreren Schritten. Zunächst analysierst du das System, dann identifizierst du Fehler und bewertest die Risiken. Schließlich erstellst du Lösungen zur Risikominderung. Diese Schritte helfen, alle Aspekte der Analyse systematisch zu bearbeiten.
In welchen Phasen eines Projekts sollte eine FMEA idealerweise durchgeführt werden?
Eine FMEA sollte idealerweise in frühen Phasen eines Projekts durchgeführt werden. Dazu gehören die Entwicklungs- und Planungsphasen. So kannst du potenzielle Risiken rechtzeitig erkennen und beheben, bevor das Produkt in die Produktion geht.
Wer ist typischerweise an der Durchführung einer FMEA beteiligt?
Typischerweise sind an der Durchführung einer FMEA mehrere Personen beteiligt. Dazu gehören Ingenieure, Qualitätssicherungsmitarbeiter und Projektmanager. Ein interdisziplinäres Team stellt sicher, dass alle relevanten Perspektiven berücksichtigt werden.
Welche verschiedenen Arten von FMEA gibt es und wie unterscheiden sie sich?
Es gibt verschiedene Arten von FMEA, darunter die Design-FMEA (DFMEA) und die Prozess-FMEA (PFMEA). DFMEA konzentriert sich auf das Design eines Produkts, während PFMEA den Produktionsprozess analysiert. Beide Methoden verfolgen das Ziel, Risiken zu identifizieren, jedoch in unterschiedlichen Kontexten.
Wie werden die Ergebnisse einer FMEA dokumentiert und kommuniziert?
Die Ergebnisse einer FMEA werden systematisch dokumentiert. Dies umfasst eine detaillierte Auflistung der identifizierten Fehler, deren Ursachen und mögliche Lösungen. Die Kommunikation erfolgt oft in Form von Berichten, die im Team geteilt werden, um sicherzustellen, dass alle Beteiligten informiert sind.
FMEA ist eine wichtige Methode zur Risikoanalyse, die Ihnen hilft, potenzielle Fehler in Ihrem Produkt oder Prozess zu erkennen. Durch die Anwendung von FMEA können Sie proaktive Maßnahmen ergreifen, um die Qualität und Sicherheit Ihrer Projekte zu erhöhen. Dies ist entscheidend, um spätere Probleme zu vermeiden und die Zufriedenheit Ihrer Kunden sicherzustellen.
Der FMEA-Prozess umfasst verschiedene Schritte, die systematisch durchgeführt werden, um Unsicherheiten zu identifizieren. Indem Sie diese Methode in Ihr Projektmanagement integrieren, können Sie gemeinsam mit einem Team wertvolle Erkenntnisse gewinnen, die die Effizienz und Effektivität Ihrer Entwicklungen steigern. Die richtige Anwendung von FMEA führt zu einer besseren Planung und einem klareren Überblick über mögliche Risiken.
Wenn Sie mehr über diese Methode und die spezifischen Abläufe erfahren möchten, sind Sie hier genau richtig. Der folgende Artikel wird Ihnen alle wichtigen Informationen und praktischen Tipps zur FMEA bieten, damit Sie die Vorteile dieser Methode optimal nutzen können.
Key Takeaways
FMEA hilft Ihnen, potenzielle Fehler frühzeitig zu identifizieren.
Ein strukturierter Prozess ist entscheidend für den Erfolg der FMEA.
Der Einsatz von FMEA steigert die Qualität und Sicherheit Ihrer Produkte.
Grundlagen der FMEA
In diesem Abschnitt wird die FMEA erklärt, einschließlich ihrer Definition, Bedeutung und ihrer historischen Entwicklung. Dies hilft Ihnen, ein besseres Verständnis für die Methode und ihre Anwendung in der Risikoanalyse zu entwickeln.
Definition und Bedeutung
Die Fehler-Möglichkeiten- und Fehler-Einfluss-Analyse (FMEA) ist eine systematische Methode zur Identifizierung und Bewertung potenzieller Fehler in einem Produkt oder Prozess. Ziel ist es, Risiken frühzeitig zu erkennen und geeignete Maßnahmen zur Vermeidung oder Minderung dieser Risiken zu ergreifen.
Die FMEA spielt eine wichtige Rolle in der Qualitätssicherung, da sie Ihnen hilft, die Sicherheit und Qualität Ihrer Produkte zu gewährleisten. Durch die frühzeitige Erkennung von Problemen können Sie kostspielige Fehler und negative Auswirkungen auf die Kundenzufriedenheit reduzieren. Ein interdisziplinäres Team führt die FMEA durch, um verschiedene Perspektiven und Fachkenntnisse in die Risikobewertung einzubeziehen.
Historie und Entwicklung der FMEA
Die FMEA-Methode wurde in den 1960er Jahren von der US-Armee zur Verbesserung der Sicherheit in militärischen Projekten entwickelt. Später wurde die Methode in der Automobilindustrie adaptiert, um die Qualität und Zuverlässigkeit von Fahrzeugen zu erhöhen.
Im Laufe der Zeit hat sich die FMEA weiterentwickelt und ist heute in vielen Branchen ein wichtiges Werkzeug für die Risikoanalyse. Sie wird häufig in der Produktentwicklung, im Maschinenbau und im Gesundheitswesen eingesetzt. Die Methode hilft Ihnen, proaktiv mit potenziellen Risiken umzugehen und Prozesse effizienter zu gestalten, was zu einer höheren Produkt- und Prozessqualität führt.
Arten der FMEA
Die Analyse der Fehlermöglichkeiten und deren Auswirkungen erfolgt in verschiedenen Arten, jede mit einem speziellen Fokus. Hier werden die Design-FMEA, Prozess-FMEA und System-FMEA betrachtet, um zu zeigen, wie sie in unterschiedlichen Kontexten angewendet werden.
Design-FMEA
Die Design-FMEA konzentriert sich auf die Entwicklung von Produkten. Ihr Ziel ist es, potenzielle Fehler in der Produktgestaltung zu identifizieren, bevor diese in die Produktion gehen. Dabei werden verschiedene Aspekte wie Materialien, Funktionen und Entwurf analysiert.
Wichtige Schritte in der Design-FMEA sind:
Identifikation von Fehlerarten: Was könnte bei Ihrem Design schiefgehen?
Bewertung der Auswirkungen: Wie wirkten sich diese Fehler auf das Produkt aus?
Risikoprioritätsnummer (RPN): Berechnung der Schwere, Auftretenswahrscheinlichkeit und Entdeckungswahrscheinlichkeit, um Risiken zu priorisieren.
Die Analyse hilft, die Qualität des Endprodukts zu sichern und teure Korrekturen in späteren Phasen zu vermeiden.
Prozess-FMEA
Die Prozess-FMEA befasst sich mit bestehenden Produktionsprozessen. Sie hilft, potenzielle Fehlerquellen innerhalb dieser Prozesse zu erkennen und die Qualität sowie Effizienz zu erhöhen. Anwendungsbeispiele sind Montage-, Fertigungs- und Prüfprozesse.
Wichtige Schritte in der Prozess-FMEA sind:
Prozessflussdiagramm: Erstellen eines Diagramms, um die einzelnen Schritte des Prozesses zu visualisieren.
Fehleranalyse: Untersuchung, bei welchen Schritten Fehler auftreten können.
Massnahmen zur Fehlervermeidung: Entwicklung von Strategien zur Minimierung identifizierter Risiken.
Mit der Prozess-FMEA verbessern Sie die Zuverlässigkeit und Sicherheit Ihrer Abläufe.
System-FMEA
Die System-FMEA wird auf Systeme angewendet, die mehrere Komponenten oder Prozesse beinhalten. Diese Methode betrachtet, wie verschiedene Teile eines Systems zusammenarbeiten und wo Fehler auftreten können.
Wichtige Aspekte der System-FMEA sind:
Systemanalyse: Verständnis der Interaktionen zwischen verschiedenen Komponenten.
Risikoabschätzung: Identifizierung der Risiken, die sich aus diesen Wechselwirkungen ergeben.
Systemintegration: Sicherstellen, dass die einzelnen Bestandteile harmonisch zusammenarbeiten.
Durch die Anwendung der System-FMEA können Sie die Gesamtzuverlässigkeit Ihres Systems steigern und das Risiko von Fehlern verringern.
FMEA-Prozess und Team
Im FMEA-Prozess spielt das Team eine entscheidende Rolle. Es besteht aus verschiedenen Mitgliedern, die unterschiedliche Perspektiven und Fachkenntnisse einbringen. Eine klare Zusammenarbeit ist erforderlich, um potenzielle Fehler und Risiken effektiv zu erkennen und zu analysieren.
Aufbau des FMEA-Teams
Ein FMEA-Team besteht in der Regel aus Fachexperten, die verschiedene Aspekte eines Produkts oder Prozesses vertreten. Dazu gehören Ingenieure, Qualitätsmanager und Produkthersteller. Der FMEA-Moderator ist ebenfalls ein wichtiger Teil des Teams. Er leitet die Diskussion, sorgt für Struktur und stellt sicher, dass alle Stimmen gehört werden.
Die Teammitglieder sollten regelmäßig in Meetings zusammenkommen, um den Fortschritt zu überprüfen und neue Erkenntnisse zu diskutieren. Diese Meetings fördern den Austausch von Ideen und stärken die Zusammenarbeit. Ein gut strukturiertes Team maximiert die Effizienz und Qualität der Fehleranalyse.
Rollen und Verantwortlichkeiten
Innerhalb des Teams hat jedes Mitglied eine spezifische Rolle. Der Moderator ist für die Gesamtdurchführung verantwortlich und hält die Gruppe auf Kurs. Ingenieure analysieren technische Risiken, während Qualitätsmanager sicherstellen, dass Standards eingehalten werden.
Jedes Teammitglied sollte klar definierte Aufgaben haben. Dies könnte Folgendes umfassen:
Datenanalyse: Sammlung und Auswertung relevanter Informationen.
Fehleridentifikation: Erkennen potenzieller Fehlerquellen.
Maßnahmenplanung: Entwicklung von Strategien zur Fehlervermeidung.
Die klare Zuweisung von Rollen fördert die Verantwortung und reduziert Missverständnisse im Team. Ein effektives FMEA-Team arbeitet eng zusammen, um alle Aspekte der Analyse abzudecken und die Qualität stetig zu verbessern.
FMEA-Ablauf
Der Ablauf einer Fehlermöglichkeits- und Einflussanalyse (FMEA) ist ein systematischer Prozess. Er umfasst wichtige Schritte und Methoden, um mögliche Fehler frühzeitig zu erkennen und Risiken zu bewerten. Dies führt zu einer besseren Kontrolle und Optimierung der Produkte und Prozesse.
Strukturanalyse
In der Strukturanalyse erfassen Sie das Produkt oder den Prozess in seiner Gesamtheit. Hierbei erstellen Sie eine Dokumentation der Struktur, die alle Komponenten und deren Beziehungen umfasst. Dies wird oft in Form von Diagrammen oder Tabellen durchgeführt.
Die Analyse hilft Ihnen, alle relevanten Teile zu identifizieren und zu verstehen. Zudem definieren Sie die Funktionen der einzelnen Komponenten. Indem Sie Schwächen in der Struktur identifizieren, können Sie gezielte Änderungen vornehmen, um die Robustheit zu erhöhen.
Funktionsanalyse
Die Funktionsanalyse folgt der Strukturanalyse und fokussiert sich auf die spezifischen Funktionen der identifizierten Komponenten. Hier prüfen Sie, ob jede Komponente ihre Aufgabe erfüllt. Sie analysieren, welche Funktionen kritisch sind und welche möglicherweise versagen können.
In dieser Phase ist es wichtig, auch die Risikoprioritätszahl (RPZ) zu bestimmen. Diese Zahl hilft Ihnen, die Wichtigkeit der jeweiligen Funktion zu bewerten. Bedenken Sie, dass eine klare Funktionsdefinition die Grundlage für die nachfolgenden Schritte der FMEA bildet.
Fehleranalyse
Die Fehleranalyse ist der letzte Schritt im FMEA-Ablauf. Hier identifizieren Sie potenzielle Fehler, die in den vorherigen Analysen aufgetreten sind. Sie bewerten die Wahrscheinlichkeit und die Auswirkungen jedes Fehlers auf das Gesamtsystem.
Jeder Fehler wird dokumentiert und hinsichtlich seiner Schwere und Häufigkeit bewertet. Durch diesen Prozess erfahren Sie, welche Fehlerkorrekturen dringend notwendig sind. Dies ermöglicht ein effektives Risikomanagement und unterstützt die Optimierung Ihres Produkts oder Prozesses.
Bewertung und Management von Risiken
Um die Qualität Ihres Produkts zu sichern und Risiken zu minimieren, ist ein systematischer Ansatz zur Risikobewertung und -management notwendig. Dieser umfasst die Risikobewertung mithilfe der Risikoprioritätszahl (RPZ) und die Umsetzung geeigneter Maßnahmen zur Risikominimierung.
Risikobewertung mit der RPZ
Die Risikoprioritätszahl (RPZ) ist ein wichtiges Werkzeug zur Bewertung von Risiken. Diese Zahl hilft Ihnen, potenzielle Fehler und deren Auswirkungen zu quantifizieren.
Die RPZ wird durch folgende Formel berechnet:
RPZ = Auftretenswahrscheinlichkeit x Schwere der Auswirkung x Entdeckungswahrscheinlichkeit
Auftretenswahrscheinlichkeit: Wie häufig der Fehler auftreten könnte.
Schwere der Auswirkung: Welche Folgen der Fehler hat.
Entdeckungswahrscheinlichkeit: Wie leicht der Fehler erkannt wird.
Mit dieser Methode können Sie Risiken priorisieren. Eine höhere RPZ zeigt an, dass ein Fehler dringender behandelt werden muss. So sichern Sie die Produktqualität und steigern die Kundenzufriedenheit.
Maßnahmen zur Risikominimierung
Nachdem Sie die Risiken bewertet haben, ist es wichtig, gezielte Maßnahmen zur Risikominderung zu ergreifen. Diese Maßnahmen sollten sich auf die wichtigsten Fehlerquellen konzentrieren.
Einige häufige Strategien sind:
Fehlervermeidung: Anpassen von Prozessen, um Fehler schon im Vorfeld zu verhindern.
Schulung: Mitarbeitende in der Fehlervermeidung trainieren.
Qualitätsmanagement: Regelmäßige Überprüfungen und Audits durchführen.
Mit diesen Maßnahmen reduzieren Sie Kosten, die durch fehlerhafte Produkte entstehen können. Gleichzeitig verbessern Sie die Produktqualität und erhöhen die Zufriedenheit Ihrer Kunden.
Häufig gestellte Fragen
In diesem Abschnitt werden häufige Fragen zur FMEA beantwortet. Es wird erklärt, was FMEA ist, welche Schritte sie umfasst und wer daran beteiligt ist. Auch die verschiedenen Arten von FMEA und ihre Dokumentation werden behandelt.
Was versteht man unter einer FMEA und welche Ziele werden damit verfolgt?
FMEA steht für Fehlermöglichkeiten- und -einflussanalyse. Mit dieser Methode identifizierst du potenzielle Fehler und deren Auswirkungen in einem Produkt oder Prozess. Die Ziele sind, die Sicherheit zu erhöhen und die Qualität zu gewährleisten, indem Probleme frühzeitig erkannt werden.
Welche Schritte umfasst der Ablauf einer FMEA-Analyse?
Die FMEA-Analyse erfolgt in mehreren Schritten. Zunächst analysierst du das System, dann identifizierst du Fehler und bewertest die Risiken. Schließlich erstellst du Lösungen zur Risikominderung. Diese Schritte helfen, alle Aspekte der Analyse systematisch zu bearbeiten.
In welchen Phasen eines Projekts sollte eine FMEA idealerweise durchgeführt werden?
Eine FMEA sollte idealerweise in frühen Phasen eines Projekts durchgeführt werden. Dazu gehören die Entwicklungs- und Planungsphasen. So kannst du potenzielle Risiken rechtzeitig erkennen und beheben, bevor das Produkt in die Produktion geht.
Wer ist typischerweise an der Durchführung einer FMEA beteiligt?
Typischerweise sind an der Durchführung einer FMEA mehrere Personen beteiligt. Dazu gehören Ingenieure, Qualitätssicherungsmitarbeiter und Projektmanager. Ein interdisziplinäres Team stellt sicher, dass alle relevanten Perspektiven berücksichtigt werden.
Welche verschiedenen Arten von FMEA gibt es und wie unterscheiden sie sich?
Es gibt verschiedene Arten von FMEA, darunter die Design-FMEA (DFMEA) und die Prozess-FMEA (PFMEA). DFMEA konzentriert sich auf das Design eines Produkts, während PFMEA den Produktionsprozess analysiert. Beide Methoden verfolgen das Ziel, Risiken zu identifizieren, jedoch in unterschiedlichen Kontexten.
Wie werden die Ergebnisse einer FMEA dokumentiert und kommuniziert?
Die Ergebnisse einer FMEA werden systematisch dokumentiert. Dies umfasst eine detaillierte Auflistung der identifizierten Fehler, deren Ursachen und mögliche Lösungen. Die Kommunikation erfolgt oft in Form von Berichten, die im Team geteilt werden, um sicherzustellen, dass alle Beteiligten informiert sind.
FMEA ist eine wichtige Methode zur Risikoanalyse, die Ihnen hilft, potenzielle Fehler in Ihrem Produkt oder Prozess zu erkennen. Durch die Anwendung von FMEA können Sie proaktive Maßnahmen ergreifen, um die Qualität und Sicherheit Ihrer Projekte zu erhöhen. Dies ist entscheidend, um spätere Probleme zu vermeiden und die Zufriedenheit Ihrer Kunden sicherzustellen.
Der FMEA-Prozess umfasst verschiedene Schritte, die systematisch durchgeführt werden, um Unsicherheiten zu identifizieren. Indem Sie diese Methode in Ihr Projektmanagement integrieren, können Sie gemeinsam mit einem Team wertvolle Erkenntnisse gewinnen, die die Effizienz und Effektivität Ihrer Entwicklungen steigern. Die richtige Anwendung von FMEA führt zu einer besseren Planung und einem klareren Überblick über mögliche Risiken.
Wenn Sie mehr über diese Methode und die spezifischen Abläufe erfahren möchten, sind Sie hier genau richtig. Der folgende Artikel wird Ihnen alle wichtigen Informationen und praktischen Tipps zur FMEA bieten, damit Sie die Vorteile dieser Methode optimal nutzen können.
Key Takeaways
FMEA hilft Ihnen, potenzielle Fehler frühzeitig zu identifizieren.
Ein strukturierter Prozess ist entscheidend für den Erfolg der FMEA.
Der Einsatz von FMEA steigert die Qualität und Sicherheit Ihrer Produkte.
Grundlagen der FMEA
In diesem Abschnitt wird die FMEA erklärt, einschließlich ihrer Definition, Bedeutung und ihrer historischen Entwicklung. Dies hilft Ihnen, ein besseres Verständnis für die Methode und ihre Anwendung in der Risikoanalyse zu entwickeln.
Definition und Bedeutung
Die Fehler-Möglichkeiten- und Fehler-Einfluss-Analyse (FMEA) ist eine systematische Methode zur Identifizierung und Bewertung potenzieller Fehler in einem Produkt oder Prozess. Ziel ist es, Risiken frühzeitig zu erkennen und geeignete Maßnahmen zur Vermeidung oder Minderung dieser Risiken zu ergreifen.
Die FMEA spielt eine wichtige Rolle in der Qualitätssicherung, da sie Ihnen hilft, die Sicherheit und Qualität Ihrer Produkte zu gewährleisten. Durch die frühzeitige Erkennung von Problemen können Sie kostspielige Fehler und negative Auswirkungen auf die Kundenzufriedenheit reduzieren. Ein interdisziplinäres Team führt die FMEA durch, um verschiedene Perspektiven und Fachkenntnisse in die Risikobewertung einzubeziehen.
Historie und Entwicklung der FMEA
Die FMEA-Methode wurde in den 1960er Jahren von der US-Armee zur Verbesserung der Sicherheit in militärischen Projekten entwickelt. Später wurde die Methode in der Automobilindustrie adaptiert, um die Qualität und Zuverlässigkeit von Fahrzeugen zu erhöhen.
Im Laufe der Zeit hat sich die FMEA weiterentwickelt und ist heute in vielen Branchen ein wichtiges Werkzeug für die Risikoanalyse. Sie wird häufig in der Produktentwicklung, im Maschinenbau und im Gesundheitswesen eingesetzt. Die Methode hilft Ihnen, proaktiv mit potenziellen Risiken umzugehen und Prozesse effizienter zu gestalten, was zu einer höheren Produkt- und Prozessqualität führt.
Arten der FMEA
Die Analyse der Fehlermöglichkeiten und deren Auswirkungen erfolgt in verschiedenen Arten, jede mit einem speziellen Fokus. Hier werden die Design-FMEA, Prozess-FMEA und System-FMEA betrachtet, um zu zeigen, wie sie in unterschiedlichen Kontexten angewendet werden.
Design-FMEA
Die Design-FMEA konzentriert sich auf die Entwicklung von Produkten. Ihr Ziel ist es, potenzielle Fehler in der Produktgestaltung zu identifizieren, bevor diese in die Produktion gehen. Dabei werden verschiedene Aspekte wie Materialien, Funktionen und Entwurf analysiert.
Wichtige Schritte in der Design-FMEA sind:
Identifikation von Fehlerarten: Was könnte bei Ihrem Design schiefgehen?
Bewertung der Auswirkungen: Wie wirkten sich diese Fehler auf das Produkt aus?
Risikoprioritätsnummer (RPN): Berechnung der Schwere, Auftretenswahrscheinlichkeit und Entdeckungswahrscheinlichkeit, um Risiken zu priorisieren.
Die Analyse hilft, die Qualität des Endprodukts zu sichern und teure Korrekturen in späteren Phasen zu vermeiden.
Prozess-FMEA
Die Prozess-FMEA befasst sich mit bestehenden Produktionsprozessen. Sie hilft, potenzielle Fehlerquellen innerhalb dieser Prozesse zu erkennen und die Qualität sowie Effizienz zu erhöhen. Anwendungsbeispiele sind Montage-, Fertigungs- und Prüfprozesse.
Wichtige Schritte in der Prozess-FMEA sind:
Prozessflussdiagramm: Erstellen eines Diagramms, um die einzelnen Schritte des Prozesses zu visualisieren.
Fehleranalyse: Untersuchung, bei welchen Schritten Fehler auftreten können.
Massnahmen zur Fehlervermeidung: Entwicklung von Strategien zur Minimierung identifizierter Risiken.
Mit der Prozess-FMEA verbessern Sie die Zuverlässigkeit und Sicherheit Ihrer Abläufe.
System-FMEA
Die System-FMEA wird auf Systeme angewendet, die mehrere Komponenten oder Prozesse beinhalten. Diese Methode betrachtet, wie verschiedene Teile eines Systems zusammenarbeiten und wo Fehler auftreten können.
Wichtige Aspekte der System-FMEA sind:
Systemanalyse: Verständnis der Interaktionen zwischen verschiedenen Komponenten.
Risikoabschätzung: Identifizierung der Risiken, die sich aus diesen Wechselwirkungen ergeben.
Systemintegration: Sicherstellen, dass die einzelnen Bestandteile harmonisch zusammenarbeiten.
Durch die Anwendung der System-FMEA können Sie die Gesamtzuverlässigkeit Ihres Systems steigern und das Risiko von Fehlern verringern.
FMEA-Prozess und Team
Im FMEA-Prozess spielt das Team eine entscheidende Rolle. Es besteht aus verschiedenen Mitgliedern, die unterschiedliche Perspektiven und Fachkenntnisse einbringen. Eine klare Zusammenarbeit ist erforderlich, um potenzielle Fehler und Risiken effektiv zu erkennen und zu analysieren.
Aufbau des FMEA-Teams
Ein FMEA-Team besteht in der Regel aus Fachexperten, die verschiedene Aspekte eines Produkts oder Prozesses vertreten. Dazu gehören Ingenieure, Qualitätsmanager und Produkthersteller. Der FMEA-Moderator ist ebenfalls ein wichtiger Teil des Teams. Er leitet die Diskussion, sorgt für Struktur und stellt sicher, dass alle Stimmen gehört werden.
Die Teammitglieder sollten regelmäßig in Meetings zusammenkommen, um den Fortschritt zu überprüfen und neue Erkenntnisse zu diskutieren. Diese Meetings fördern den Austausch von Ideen und stärken die Zusammenarbeit. Ein gut strukturiertes Team maximiert die Effizienz und Qualität der Fehleranalyse.
Rollen und Verantwortlichkeiten
Innerhalb des Teams hat jedes Mitglied eine spezifische Rolle. Der Moderator ist für die Gesamtdurchführung verantwortlich und hält die Gruppe auf Kurs. Ingenieure analysieren technische Risiken, während Qualitätsmanager sicherstellen, dass Standards eingehalten werden.
Jedes Teammitglied sollte klar definierte Aufgaben haben. Dies könnte Folgendes umfassen:
Datenanalyse: Sammlung und Auswertung relevanter Informationen.
Fehleridentifikation: Erkennen potenzieller Fehlerquellen.
Maßnahmenplanung: Entwicklung von Strategien zur Fehlervermeidung.
Die klare Zuweisung von Rollen fördert die Verantwortung und reduziert Missverständnisse im Team. Ein effektives FMEA-Team arbeitet eng zusammen, um alle Aspekte der Analyse abzudecken und die Qualität stetig zu verbessern.
FMEA-Ablauf
Der Ablauf einer Fehlermöglichkeits- und Einflussanalyse (FMEA) ist ein systematischer Prozess. Er umfasst wichtige Schritte und Methoden, um mögliche Fehler frühzeitig zu erkennen und Risiken zu bewerten. Dies führt zu einer besseren Kontrolle und Optimierung der Produkte und Prozesse.
Strukturanalyse
In der Strukturanalyse erfassen Sie das Produkt oder den Prozess in seiner Gesamtheit. Hierbei erstellen Sie eine Dokumentation der Struktur, die alle Komponenten und deren Beziehungen umfasst. Dies wird oft in Form von Diagrammen oder Tabellen durchgeführt.
Die Analyse hilft Ihnen, alle relevanten Teile zu identifizieren und zu verstehen. Zudem definieren Sie die Funktionen der einzelnen Komponenten. Indem Sie Schwächen in der Struktur identifizieren, können Sie gezielte Änderungen vornehmen, um die Robustheit zu erhöhen.
Funktionsanalyse
Die Funktionsanalyse folgt der Strukturanalyse und fokussiert sich auf die spezifischen Funktionen der identifizierten Komponenten. Hier prüfen Sie, ob jede Komponente ihre Aufgabe erfüllt. Sie analysieren, welche Funktionen kritisch sind und welche möglicherweise versagen können.
In dieser Phase ist es wichtig, auch die Risikoprioritätszahl (RPZ) zu bestimmen. Diese Zahl hilft Ihnen, die Wichtigkeit der jeweiligen Funktion zu bewerten. Bedenken Sie, dass eine klare Funktionsdefinition die Grundlage für die nachfolgenden Schritte der FMEA bildet.
Fehleranalyse
Die Fehleranalyse ist der letzte Schritt im FMEA-Ablauf. Hier identifizieren Sie potenzielle Fehler, die in den vorherigen Analysen aufgetreten sind. Sie bewerten die Wahrscheinlichkeit und die Auswirkungen jedes Fehlers auf das Gesamtsystem.
Jeder Fehler wird dokumentiert und hinsichtlich seiner Schwere und Häufigkeit bewertet. Durch diesen Prozess erfahren Sie, welche Fehlerkorrekturen dringend notwendig sind. Dies ermöglicht ein effektives Risikomanagement und unterstützt die Optimierung Ihres Produkts oder Prozesses.
Bewertung und Management von Risiken
Um die Qualität Ihres Produkts zu sichern und Risiken zu minimieren, ist ein systematischer Ansatz zur Risikobewertung und -management notwendig. Dieser umfasst die Risikobewertung mithilfe der Risikoprioritätszahl (RPZ) und die Umsetzung geeigneter Maßnahmen zur Risikominimierung.
Risikobewertung mit der RPZ
Die Risikoprioritätszahl (RPZ) ist ein wichtiges Werkzeug zur Bewertung von Risiken. Diese Zahl hilft Ihnen, potenzielle Fehler und deren Auswirkungen zu quantifizieren.
Die RPZ wird durch folgende Formel berechnet:
RPZ = Auftretenswahrscheinlichkeit x Schwere der Auswirkung x Entdeckungswahrscheinlichkeit
Auftretenswahrscheinlichkeit: Wie häufig der Fehler auftreten könnte.
Schwere der Auswirkung: Welche Folgen der Fehler hat.
Entdeckungswahrscheinlichkeit: Wie leicht der Fehler erkannt wird.
Mit dieser Methode können Sie Risiken priorisieren. Eine höhere RPZ zeigt an, dass ein Fehler dringender behandelt werden muss. So sichern Sie die Produktqualität und steigern die Kundenzufriedenheit.
Maßnahmen zur Risikominimierung
Nachdem Sie die Risiken bewertet haben, ist es wichtig, gezielte Maßnahmen zur Risikominderung zu ergreifen. Diese Maßnahmen sollten sich auf die wichtigsten Fehlerquellen konzentrieren.
Einige häufige Strategien sind:
Fehlervermeidung: Anpassen von Prozessen, um Fehler schon im Vorfeld zu verhindern.
Schulung: Mitarbeitende in der Fehlervermeidung trainieren.
Qualitätsmanagement: Regelmäßige Überprüfungen und Audits durchführen.
Mit diesen Maßnahmen reduzieren Sie Kosten, die durch fehlerhafte Produkte entstehen können. Gleichzeitig verbessern Sie die Produktqualität und erhöhen die Zufriedenheit Ihrer Kunden.
Häufig gestellte Fragen
In diesem Abschnitt werden häufige Fragen zur FMEA beantwortet. Es wird erklärt, was FMEA ist, welche Schritte sie umfasst und wer daran beteiligt ist. Auch die verschiedenen Arten von FMEA und ihre Dokumentation werden behandelt.
Was versteht man unter einer FMEA und welche Ziele werden damit verfolgt?
FMEA steht für Fehlermöglichkeiten- und -einflussanalyse. Mit dieser Methode identifizierst du potenzielle Fehler und deren Auswirkungen in einem Produkt oder Prozess. Die Ziele sind, die Sicherheit zu erhöhen und die Qualität zu gewährleisten, indem Probleme frühzeitig erkannt werden.
Welche Schritte umfasst der Ablauf einer FMEA-Analyse?
Die FMEA-Analyse erfolgt in mehreren Schritten. Zunächst analysierst du das System, dann identifizierst du Fehler und bewertest die Risiken. Schließlich erstellst du Lösungen zur Risikominderung. Diese Schritte helfen, alle Aspekte der Analyse systematisch zu bearbeiten.
In welchen Phasen eines Projekts sollte eine FMEA idealerweise durchgeführt werden?
Eine FMEA sollte idealerweise in frühen Phasen eines Projekts durchgeführt werden. Dazu gehören die Entwicklungs- und Planungsphasen. So kannst du potenzielle Risiken rechtzeitig erkennen und beheben, bevor das Produkt in die Produktion geht.
Wer ist typischerweise an der Durchführung einer FMEA beteiligt?
Typischerweise sind an der Durchführung einer FMEA mehrere Personen beteiligt. Dazu gehören Ingenieure, Qualitätssicherungsmitarbeiter und Projektmanager. Ein interdisziplinäres Team stellt sicher, dass alle relevanten Perspektiven berücksichtigt werden.
Welche verschiedenen Arten von FMEA gibt es und wie unterscheiden sie sich?
Es gibt verschiedene Arten von FMEA, darunter die Design-FMEA (DFMEA) und die Prozess-FMEA (PFMEA). DFMEA konzentriert sich auf das Design eines Produkts, während PFMEA den Produktionsprozess analysiert. Beide Methoden verfolgen das Ziel, Risiken zu identifizieren, jedoch in unterschiedlichen Kontexten.
Wie werden die Ergebnisse einer FMEA dokumentiert und kommuniziert?
Die Ergebnisse einer FMEA werden systematisch dokumentiert. Dies umfasst eine detaillierte Auflistung der identifizierten Fehler, deren Ursachen und mögliche Lösungen. Die Kommunikation erfolgt oft in Form von Berichten, die im Team geteilt werden, um sicherzustellen, dass alle Beteiligten informiert sind.

am Freitag, 2. August 2024