Lean Production: Das Konzept einfach erklärt und seine Vorteile für die Effizienzsteigerung
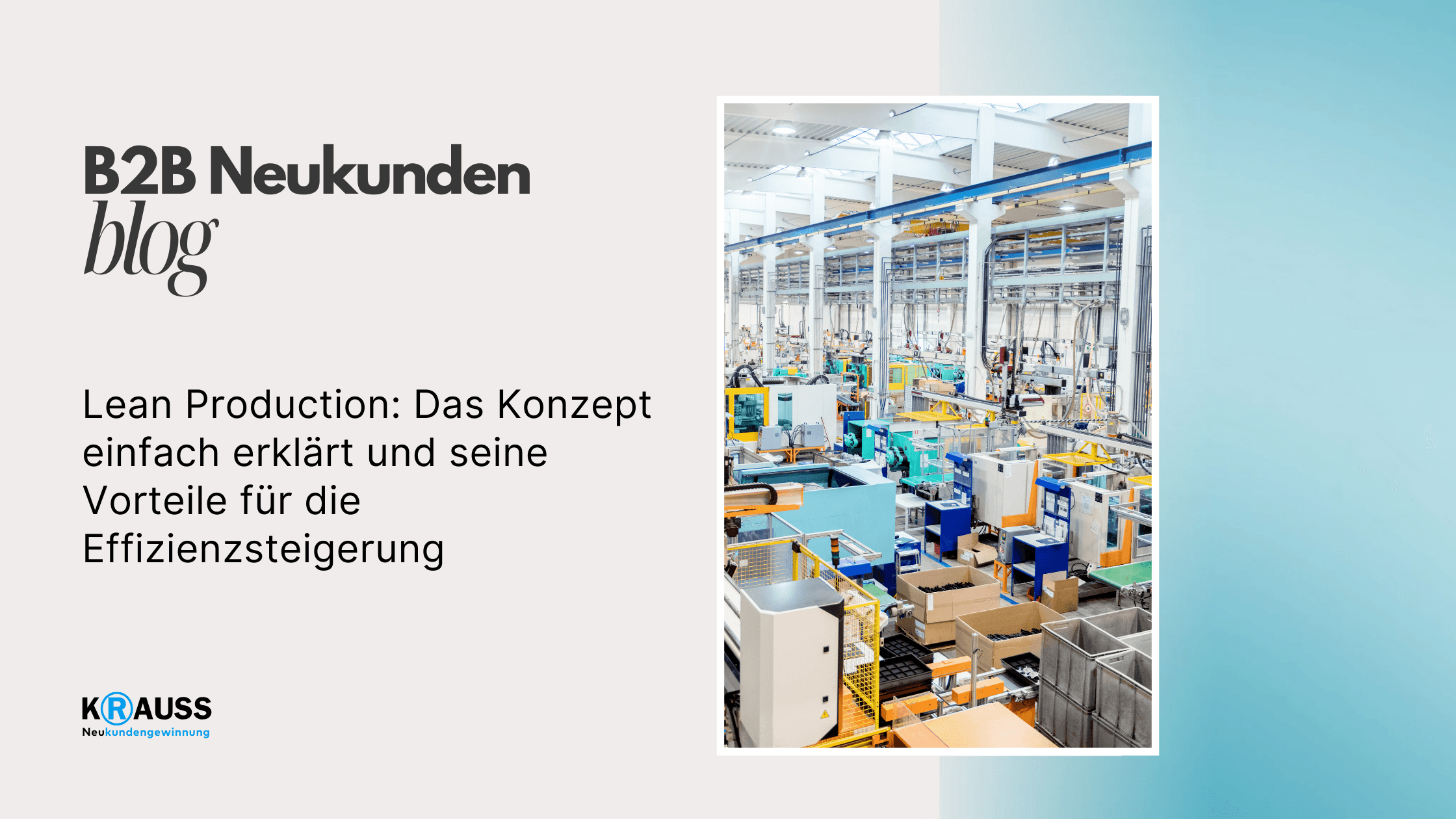
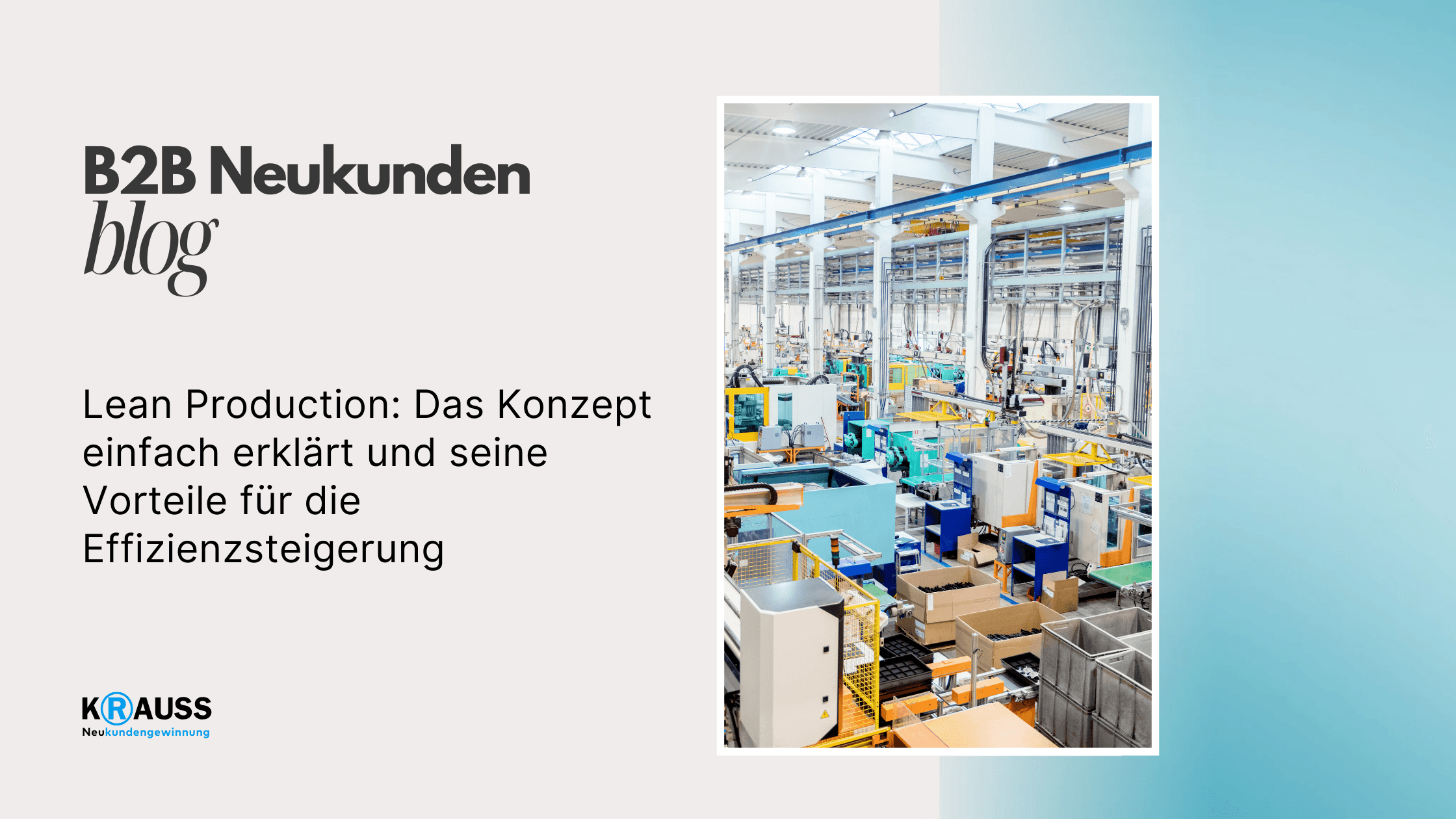
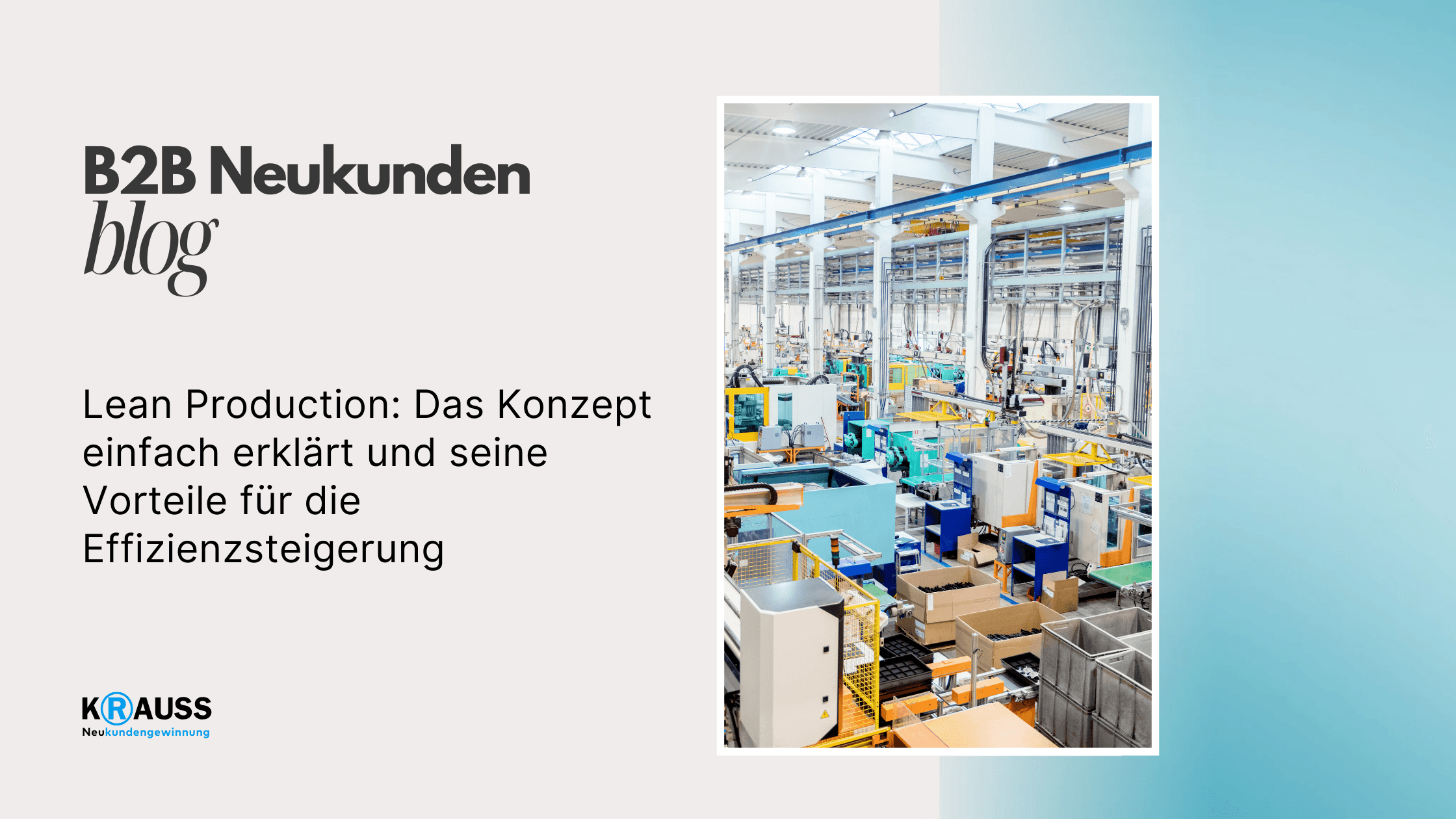

Montag, 2. September 2024
•
5 Min. Lesezeit
•
Lean Production ist ein modernes Konzept, das in der Industrie für mehr Effizienz und weniger Verschwendung sorgt. Indem Sie die Prinzipien der Lean Production anwenden, können Sie Ihre Produktionsprozesse optimieren und die Qualität Ihrer Produkte steigern. Dieses Konzept hat sich besonders in Unternehmen etabliert, die in einem wettbewerbsintensiven Umfeld agieren.
In diesem Artikel erhalten Sie einen klaren Überblick über die Grundlagen und Prinzipien von Lean Production. Sie werden lernen, wie Unternehmen diese Methoden erfolgreich umsetzen und welche Rolle die Mitarbeiter und die Unternehmenskultur dabei spielen. Zudem werden Ergebnisse und Fallbeispiele betrachtet, die die positiven Effekte von Lean Management aufzeigen.
Sehen Sie sich die verschiedenen Aspekte an, die Lean Production zu einem unverzichtbaren Teil der modernen Produktion machen. Entdecken Sie, wie Sie durch den gezielten Einsatz dieser Strategien Ihre Effizienz steigern und Verschwendung reduzieren können.
Key Takeaways
Lean Production verbessert die Effizienz in der Industrie.
Mitarbeiter und Unternehmenskultur sind entscheidend für den Erfolg.
Fallbeispiele zeigen die positiven Ergebnisse der Umsetzung.
Grundlagen und Prinzipien der Lean Production
Lean Production umfasst wichtige Prinzipien, die darauf abzielen, die Effizienz in der Produktion zu steigern. Die folgenden Aspekte konzentrieren sich auf das Minimieren von Verschwendung, die Anwendung von Pull- und Fluss-Prinzipien sowie die kontinuierliche Verbesserung.
Verschwendung minimieren - Die 7 Muda
Eines der Hauptziele von Lean Production ist es, Verschwendung, auch bekannt als Muda, zu reduzieren. Die 7 Muda sind:
Überproduktion: Mehr produzieren als nötig.
Warten: Verzögerungen in der Produktion.
Transport: Unnötige Bewegungen von Materialien.
Überbearbeitung: Zuviel Aufwand für einfache Aufgaben.
Bestände: Hohe Lagerbestände, die nicht benötigt werden.
Bewegung: Unnötige Bewegungen von Arbeitskräften.
Fehler: Mängel, die Nacharbeit erfordern.
Indem Sie diese Arten von Muda erkennen und beseitigen, verbessern Sie die Qualität und Effizienz Ihrer Produktionsprozesse.
Das Pull-Prinzip und Fluss-Prinzip
Das Pull-Prinzip ist eine zentrale Methode der Lean Production. Es bedeutet, dass Produktion nur dann erfolgt, wenn es eine Nachfrage gibt. Dies verhindert Überproduktion und sorgt für optimalen Ressourcenverbrauch.
Das Fluss-Prinzip zielt darauf ab, dass Materialien und Informationen ohne Unterbrechungen durch den Produktionsprozess fließen. Ziel ist es, Leerlaufzeiten zu minimieren und den gesamten Prozess effizient zu gestalten. Beide Prinzipien helfen, die Produktionszeit zu verringern und die Qualität zu steigern.
Kontinuierliche Verbesserung - Kaizen
Kaizen ist ein japanischer Begriff, der „kontinuierliche Verbesserung“ bedeutet. In der Lean Production ermutigt Kaizen alle Mitarbeiter, Vorschläge zur Verbesserung zu unterbreiten. Dies kann kleinen Veränderungen in der Arbeitsweise bis hin zu größeren Prozessanpassungen reichen.
Der Schlüssel zu Kaizen ist, regelmäßig kleine Schritte zur Optimierung zu unternehmen. So schaffen Sie eine Unternehmenskultur, in der ständige Verbesserungen standardmäßig integriert sind. Diese Herangehensweise trägt dazu bei, Fehler zu reduzieren und die Qualität zu verbessern.
Wertstromanalyse und -design
Die Wertstromanalyse ist ein Werkzeug zur Identifikation und Reduzierung von Verschwendung. Sie ermöglicht es Ihnen, den gesamten Prozess von der Idee bis zum Endprodukt zu visualisieren. Dabei können nicht wertschöpfende Schritte erkannt und eliminiert werden.
Das Wertstromdesign hingegen hilft, zukünftige Prozesse zu planen, die effizienter sind. Es zeigt, wie jeder Schritt im Produktionsprozess zur Wertschöpfung beiträgt und wo Optimierungen notwendig sind. So verbessern Sie sowohl Effizienz als auch Qualität der Produktionsabläufe.
Umsetzung der Lean Production im Betrieb
Die Umsetzung von Lean Production im Betrieb erfordert verschiedene spezifische Methoden. Diese Methoden helfen, Prozesse zu optimieren, Ressourcen effizient einzusetzen und Verschwendung zu minimieren. Wichtige Aspekte sind die Organisation am Arbeitsplatz, der Materialfluss und die Standardisierung von Abläufen.
5S-Methode
Die 5S-Methode steht für die fünf Schritte: Sortieren, Sitzen, Säubern, Standardisieren und Selbstdiziplin. Diese Schritte helfen, den Arbeitsplatz zu organisieren und beschleunigen die Produktionsprozesse.
Sortieren: Entfernen Sie unnötige Gegenstände, damit nur das bleibt, was wirklich benötigt wird.
Sitzen: Organisieren Sie das Arbeitsumfeld so, dass alles einfach erreichbar ist.
Säubern: Halten Sie den Arbeitsplatz sauber, um Fehler und Ausschuss zu vermeiden.
Standardisieren: Erstellen Sie klare Standards für alle Prozesse.
Selbstdiziplin: Fördern Sie eine Kultur, in der Mitarbeiter selbst für Ordnung sorgen.
Durch die Anwendung von 5S können Sie die Effizienz und Produktivität auf dem Arbeitsplatz erheblich steigern.
Kanban-System
Das Kanban-System ist ein visuelles Management-Tool, das den Materialfluss und die Produktion steuert. Mit Kanban können Sie den Bedarf an Materialien und Personal bedarfsorientiert planen.
Visualisierung: Nutzen Sie Tafeln oder Karten, um den Status von Aufträgen sichtbar zu machen.
Just-in-time: Stellen Sie sicher, dass Materialien und Produkte genau dann bereit sind, wenn sie benötigt werden, um Transportkosten und Lagerhaltung zu minimieren.
Flexibilität: Passen Sie die Produktion schnell an Veränderungen in der Nachfrage an, ohne viel Aufwand.
Diese Methode minimiert nicht nur Verschwendung, sondern verbessert auch die Kommunikation unter den Mitarbeitern.
Poka Yoke
Poka Yoke oder „Fehlervermeidung“ zielt darauf ab, menschliche Fehler im Produktionsprozess zu verhindern. Es handelt sich um einfache, oft mechanische Vorrichtungen oder Prozesse, die helfen, Fehler rechtzeitig zu erkennen.
Vorrichtungen: Verwenden Sie einfache Hilfsmittel, die sicherstellen, dass Teile nur auf eine Weise zusammengebaut werden können.
Prüfzellen: Integrieren Sie Prüfstationen, an denen Produkte auf Fehler überprüft werden.
Schulung: Schulen Sie Ihre Mitarbeiter, wie sie Poka Yoke-Prinzipien in ihren Aufgaben anwenden können.
Durch Poka Yoke reduzieren Sie den Ausschuss und verbessern die Qualität der Produkte.
Heijunka - Produktionsnivellierung
Heijunka bedeutet Produktionsnivellierung und beschäftigt sich mit der gleichmäßigen Verteilung von Arbeitslast und Produktionsvolumen. Dies hilft, Überlastung zu vermeiden.
Gleichmäßige Arbeit: Verteilen Sie die Produktionsaufträge über den Tag oder die Woche, um Spitzen und Täler zu vermeiden.
Bedarfsgerechte Planung: Planen Sie die Produktion basierend auf der tatsächlichen Nachfrage, um Überproduktion zu reduzieren.
Mitarbeiterförderung: Involvieren Sie Mitarbeiter in den Prozess, um Vorschläge zur Verbesserung der Arbeitsabläufe zu erhalten.
Die Anwendung von Heijunka führt zu einer stabilen Produktion und einer besseren Auslastung Ihrer Ressourcen.
Effizienzsteigerung durch Lean Management
Lean Management hilft dir, die Effizienz in der Produktion zu steigern. Es konzentriert sich auf die Minimierung von Verschwendung und die Verbesserung von Prozessen. Die Schwerpunkte liegen auf Just-in-Time-Produktion, der Optimierung des Materialflusses und dem kontinuierlichen Verbesserungsprozess (KVP).
Just-in-Time Produktion
Die Just-in-Time (JIT) Produktion ist ein wichtiger Ansatz im Lean Management. Hierbei wird Material genau dann geliefert, wenn es benötigt wird. Dadurch vermeidest du Überproduktion und Lagerkosten.
Durch JIT kannst du Ressourcen besser nutzen, da du nur das produzieren lässt, was aktuell nachgefragt wird. Dies führt nicht nur zu weniger Lagerbestand, sondern steigert auch die Flexibilität deiner Produktion.
Einigen Unternehmen gelingt es, ihre Produktionszeiten um bis zu 50 % zu verkürzen, wenn sie den JIT-Ansatz richtig umsetzen. Das bedeutet, dass du schneller auf Marktentwicklungen reagieren kannst.
Optimierung des Materialflusses
Ein effektiver Materialfluss ist entscheidend für die Effizienz deiner Produktion. Du solltest sicherstellen, dass Materialien und Produkte reibungslos durch den Produktionsprozess fließen.
Dazu gehört die Planung von Transportwegen und die Minimierung von Wartezeiten in der Produktion. Eine gute Logistik ist notwendig, um den Materialfluss zu verbessern.
Durch den Einsatz von visuellen Management-Tools kannst du Engpässe schnell erkennen und beheben. Beispielsweise können klare Markierungen und Schilder dir helfen, den Materialfluss zu steuern und Überlastungen zu vermeiden.
PDCA- und KVP-Zyklen
Der PDCA-Zyklus und KVP sind essentielle Werkzeuge im Lean Management. PDCA steht für Plan-Do-Check-Act und beschreibt einen kontinuierlichen Verbesserungsprozess.
Mit diesem Ansatz planst du Veränderungen, setzt sie um, überprüfst die Ergebnisse und nimmst Anpassungen vor. Dies fördert eine Kultur der ständigen Verbesserung.
KVP bedeutet, dass jeder Mitarbeiter aktiv in den Verbesserungsprozess einbezogen wird. Du kannst regelmäßige Meetings abhalten, um Ideen zu sammeln und Lösungen zu entwickeln, die die Effizienz weiter steigern.
Gemeinsam führen diese Methoden dazu, dass du häufige Probleme effizient identifizierst und löst, was langfristig die Produktivität erhöht.
Die Rolle der Mitarbeiter und Unternehmenskultur
Mitarbeiter spielen eine entscheidende Rolle in der Lean Production. Ihr Engagement und ihre Fähigkeiten sind wichtig, um Verschwendung zu minimieren und die Effizienz zu steigern.
Eine starke Unternehmenskultur fördert Teamarbeit. Wenn Mitarbeiter zusammenarbeiten, können sie Prozesse besser verstehen und optimieren. Offene Kommunikation ist dabei entscheidend.
Schulungen helfen, das Wissen über Lean-Methoden zu verbreiten. Gut ausgebildete Mitarbeiter können Probleme schneller erkennen und Lösungen finden. Regelmäßige Weiterbildung stärkt das Vertrauen in die Fähigkeiten des Teams.
Führungskräfte müssen eine unterstützende Rolle übernehmen. Sie sollten die Mitarbeiter in Entscheidungen einbeziehen und ein Umfeld schaffen, in dem Vorschläge willkommen sind. Partizipation fördert Motivation und Kreativität.
In der Lean Production geht es nicht nur um Prozesse, sondern auch um das Wohlbefinden der Mitarbeiter. Eine positive Unternehmenskultur führt zu höherer Zufriedenheit und weniger Fluktuation.
Zusammengefasst ist die Rolle der Mitarbeiter und der Unternehmenskultur für den Erfolg der Lean Production unverzichtbar. Engagierte Mitarbeiter und eine unterstützende Kultur sind Schlüssel zu einer effektiven Produktionsumgebung.
Lean Production Ergebnisse und Fallbeispiele
Lean Production führt zu bedeutenden Veränderungen in der Art und Weise, wie Unternehmen produzieren. Die folgenden Aspekte zeigen, wie Lean-Methoden die Produktqualität steigern, Durchlaufzeiten und Bestände reduzieren sowie die Kundenzufriedenheit erhöhen. Zudem werden praktische Fallstudien, insbesondere aus der Automobilindustrie, betrachtet.
Steigerung der Produktqualität
Durch die Implementierung von Lean Production steht die Produktqualität im Vordergrund. Methoden wie 5S (Sortieren, Setzen, Säubern, Standardisieren, Selbstdisziplin) sorgen für einen organisierten Arbeitsplatz, der Fehlerquellen minimiert.
Zusätzlich werden Qualitätskontrollen in jeder Produktionsphase durchgeführt. Dies führt dazu, dass Probleme frühzeitig erkannt werden.
Die konstante Verbesserung (Kaizen) fördert eine Kultur, in der Mitarbeiter Vorschläge zur Qualitätssicherung einbringen. Diese Maßnahmen helfen, nicht nur die Qualität des Endprodukts zu steigern, sondern auch die Zufriedenheit der Kunden zu erhöhen.
Reduktion von Durchlaufzeiten und Beständen
Ein zentrales Ziel von Lean Production ist die Reduktion der Durchlaufzeiten. Durch die Analyse von Arbeitsabläufen können Engpässe identifiziert und beseitigt werden.
Die Einführung der just-in-time-Produktion trägt dazu bei, dass Materialien nur bei Bedarf bereitgestellt werden. Dadurch werden hohe Lagerbestände vermieden.
Ein Beispiel sind Kanban-Systeme, die den Fluss von Materialien steuern und sicherstellen, dass nur die benötigten Mengen produziert werden. Das reduziert sowohl die Durchlaufzeiten als auch die Lagerkosten und steigert die Effizienz.
Erhöhung der Kundenzufriedenheit
Kundenzufriedenheit ist entscheidend für den Erfolg eines Unternehmens. Lean Production bietet verschiedene Ansätze, um Kundenbedürfnisse besser zu erfüllen. Engere Zusammenarbeit mit den Kunden hilft, deren Wünsche zu verstehen.
Durch die kürzeren Durchlaufzeiten können Produkte schneller geliefert werden.
Zusätzlich tragen verbesserte Produktqualitäten zur Steigerung der Kundenzufriedenheit bei. Wenn die Wünsche der Kunden erfüllt werden, stärkt das die Kundenbindung und fördert positive Bewertungen. Dies führt langfristig zu einem Wettbewerbsvorteil.
Fallstudien aus der Automobilindustrie
Die Automobilindustrie ist ein gutes Beispiel für erfolgreiche Lean-Implementierungen. Unternehmen wie Toyota revolutionierten das Produktionsmodell mit Lean-Methoden.
Ein konkretes Beispiel ist die Einführung des Toyota Production System (TPS). Dieses System fokussiert sich auf kontinuierliche Verbesserung und Verschlankung von Prozessen.
Zusätzlich haben viele Hersteller die Kaizen-Philosophie übernommen, um Mitarbeiter aktiv in den Verbesserungsprozess einzubeziehen. Die Ergebnisse sind deutlich: weniger Fehler, höhere Qualität und gesteigerte Effizienz.
Diese Fallstudien zeigen, wie Lean Production nicht nur die Prozesse optimiert, sondern auch die gesamte Branche voranbringt.
Häufig gestellte Fragen
In diesem Abschnitt werden grundlegende Fragen zur Lean Production behandelt. Dabei geht es um Definitionen, Vorteile, mögliche Nachteile, angewandte Methoden sowie die Hauptziele des Konzepts.
Was versteht man unter dem Begriff Lean Production?
Lean Production bezeichnet ein Konzept zur Prozessoptimierung in der Produktion. Es zielt darauf ab, Verschwendung zu minimieren und den Einsatz von Ressourcen wie Personal und Materialien zu optimieren.
Welche Vorteile bietet das Lean Production Konzept?
Das Lean Production Konzept bietet mehrere Vorteile. Dazu gehören eine höhere Effizienz, geringere Kosten und eine verbesserte Produktqualität. Unternehmen können zudem flexibler auf Kundenbedürfnisse reagieren.
Welche Nachteile können sich durch Lean Production ergeben?
Mögliche Nachteile der Lean Production sind Engpässe und höhere Drucksituationen für die Mitarbeiter. In manchen Fällen kann es auch zu einer Überoptimierung führen, die die Kreativität einschränkt.
Welche Methoden werden in der Lean Production angewandt?
In der Lean Production kommen verschiedene Methoden zum Einsatz. Dazu zählen die 5S-Methode, Kaizen und das Just-in-Time-System. Diese Methoden helfen dabei, Prozesse kontinuierlich zu verbessern.
Wie definiert sich das Lean-Konzept im Produktionskontext?
Im Produktionskontext bedeutet Lean, Ressourcen so effizient wie möglich zu nutzen. Es geht darum, alle Prozesse zu überprüfen und zu verbessern, um Abfälle zu reduzieren und den Wert für den Kunden zu steigern.
Welche Hauptziele verfolgt Lean Production?
Die Hauptziele von Lean Production sind die Maximierung der Effizienz und die Steigerung der Qualität. Unternehmen sollen durch die Reduzierung von Verschwendung und den optimalen Einsatz von Ressourcen wettbewerbsfähiger werden.
Lean Production ist ein modernes Konzept, das in der Industrie für mehr Effizienz und weniger Verschwendung sorgt. Indem Sie die Prinzipien der Lean Production anwenden, können Sie Ihre Produktionsprozesse optimieren und die Qualität Ihrer Produkte steigern. Dieses Konzept hat sich besonders in Unternehmen etabliert, die in einem wettbewerbsintensiven Umfeld agieren.
In diesem Artikel erhalten Sie einen klaren Überblick über die Grundlagen und Prinzipien von Lean Production. Sie werden lernen, wie Unternehmen diese Methoden erfolgreich umsetzen und welche Rolle die Mitarbeiter und die Unternehmenskultur dabei spielen. Zudem werden Ergebnisse und Fallbeispiele betrachtet, die die positiven Effekte von Lean Management aufzeigen.
Sehen Sie sich die verschiedenen Aspekte an, die Lean Production zu einem unverzichtbaren Teil der modernen Produktion machen. Entdecken Sie, wie Sie durch den gezielten Einsatz dieser Strategien Ihre Effizienz steigern und Verschwendung reduzieren können.
Key Takeaways
Lean Production verbessert die Effizienz in der Industrie.
Mitarbeiter und Unternehmenskultur sind entscheidend für den Erfolg.
Fallbeispiele zeigen die positiven Ergebnisse der Umsetzung.
Grundlagen und Prinzipien der Lean Production
Lean Production umfasst wichtige Prinzipien, die darauf abzielen, die Effizienz in der Produktion zu steigern. Die folgenden Aspekte konzentrieren sich auf das Minimieren von Verschwendung, die Anwendung von Pull- und Fluss-Prinzipien sowie die kontinuierliche Verbesserung.
Verschwendung minimieren - Die 7 Muda
Eines der Hauptziele von Lean Production ist es, Verschwendung, auch bekannt als Muda, zu reduzieren. Die 7 Muda sind:
Überproduktion: Mehr produzieren als nötig.
Warten: Verzögerungen in der Produktion.
Transport: Unnötige Bewegungen von Materialien.
Überbearbeitung: Zuviel Aufwand für einfache Aufgaben.
Bestände: Hohe Lagerbestände, die nicht benötigt werden.
Bewegung: Unnötige Bewegungen von Arbeitskräften.
Fehler: Mängel, die Nacharbeit erfordern.
Indem Sie diese Arten von Muda erkennen und beseitigen, verbessern Sie die Qualität und Effizienz Ihrer Produktionsprozesse.
Das Pull-Prinzip und Fluss-Prinzip
Das Pull-Prinzip ist eine zentrale Methode der Lean Production. Es bedeutet, dass Produktion nur dann erfolgt, wenn es eine Nachfrage gibt. Dies verhindert Überproduktion und sorgt für optimalen Ressourcenverbrauch.
Das Fluss-Prinzip zielt darauf ab, dass Materialien und Informationen ohne Unterbrechungen durch den Produktionsprozess fließen. Ziel ist es, Leerlaufzeiten zu minimieren und den gesamten Prozess effizient zu gestalten. Beide Prinzipien helfen, die Produktionszeit zu verringern und die Qualität zu steigern.
Kontinuierliche Verbesserung - Kaizen
Kaizen ist ein japanischer Begriff, der „kontinuierliche Verbesserung“ bedeutet. In der Lean Production ermutigt Kaizen alle Mitarbeiter, Vorschläge zur Verbesserung zu unterbreiten. Dies kann kleinen Veränderungen in der Arbeitsweise bis hin zu größeren Prozessanpassungen reichen.
Der Schlüssel zu Kaizen ist, regelmäßig kleine Schritte zur Optimierung zu unternehmen. So schaffen Sie eine Unternehmenskultur, in der ständige Verbesserungen standardmäßig integriert sind. Diese Herangehensweise trägt dazu bei, Fehler zu reduzieren und die Qualität zu verbessern.
Wertstromanalyse und -design
Die Wertstromanalyse ist ein Werkzeug zur Identifikation und Reduzierung von Verschwendung. Sie ermöglicht es Ihnen, den gesamten Prozess von der Idee bis zum Endprodukt zu visualisieren. Dabei können nicht wertschöpfende Schritte erkannt und eliminiert werden.
Das Wertstromdesign hingegen hilft, zukünftige Prozesse zu planen, die effizienter sind. Es zeigt, wie jeder Schritt im Produktionsprozess zur Wertschöpfung beiträgt und wo Optimierungen notwendig sind. So verbessern Sie sowohl Effizienz als auch Qualität der Produktionsabläufe.
Umsetzung der Lean Production im Betrieb
Die Umsetzung von Lean Production im Betrieb erfordert verschiedene spezifische Methoden. Diese Methoden helfen, Prozesse zu optimieren, Ressourcen effizient einzusetzen und Verschwendung zu minimieren. Wichtige Aspekte sind die Organisation am Arbeitsplatz, der Materialfluss und die Standardisierung von Abläufen.
5S-Methode
Die 5S-Methode steht für die fünf Schritte: Sortieren, Sitzen, Säubern, Standardisieren und Selbstdiziplin. Diese Schritte helfen, den Arbeitsplatz zu organisieren und beschleunigen die Produktionsprozesse.
Sortieren: Entfernen Sie unnötige Gegenstände, damit nur das bleibt, was wirklich benötigt wird.
Sitzen: Organisieren Sie das Arbeitsumfeld so, dass alles einfach erreichbar ist.
Säubern: Halten Sie den Arbeitsplatz sauber, um Fehler und Ausschuss zu vermeiden.
Standardisieren: Erstellen Sie klare Standards für alle Prozesse.
Selbstdiziplin: Fördern Sie eine Kultur, in der Mitarbeiter selbst für Ordnung sorgen.
Durch die Anwendung von 5S können Sie die Effizienz und Produktivität auf dem Arbeitsplatz erheblich steigern.
Kanban-System
Das Kanban-System ist ein visuelles Management-Tool, das den Materialfluss und die Produktion steuert. Mit Kanban können Sie den Bedarf an Materialien und Personal bedarfsorientiert planen.
Visualisierung: Nutzen Sie Tafeln oder Karten, um den Status von Aufträgen sichtbar zu machen.
Just-in-time: Stellen Sie sicher, dass Materialien und Produkte genau dann bereit sind, wenn sie benötigt werden, um Transportkosten und Lagerhaltung zu minimieren.
Flexibilität: Passen Sie die Produktion schnell an Veränderungen in der Nachfrage an, ohne viel Aufwand.
Diese Methode minimiert nicht nur Verschwendung, sondern verbessert auch die Kommunikation unter den Mitarbeitern.
Poka Yoke
Poka Yoke oder „Fehlervermeidung“ zielt darauf ab, menschliche Fehler im Produktionsprozess zu verhindern. Es handelt sich um einfache, oft mechanische Vorrichtungen oder Prozesse, die helfen, Fehler rechtzeitig zu erkennen.
Vorrichtungen: Verwenden Sie einfache Hilfsmittel, die sicherstellen, dass Teile nur auf eine Weise zusammengebaut werden können.
Prüfzellen: Integrieren Sie Prüfstationen, an denen Produkte auf Fehler überprüft werden.
Schulung: Schulen Sie Ihre Mitarbeiter, wie sie Poka Yoke-Prinzipien in ihren Aufgaben anwenden können.
Durch Poka Yoke reduzieren Sie den Ausschuss und verbessern die Qualität der Produkte.
Heijunka - Produktionsnivellierung
Heijunka bedeutet Produktionsnivellierung und beschäftigt sich mit der gleichmäßigen Verteilung von Arbeitslast und Produktionsvolumen. Dies hilft, Überlastung zu vermeiden.
Gleichmäßige Arbeit: Verteilen Sie die Produktionsaufträge über den Tag oder die Woche, um Spitzen und Täler zu vermeiden.
Bedarfsgerechte Planung: Planen Sie die Produktion basierend auf der tatsächlichen Nachfrage, um Überproduktion zu reduzieren.
Mitarbeiterförderung: Involvieren Sie Mitarbeiter in den Prozess, um Vorschläge zur Verbesserung der Arbeitsabläufe zu erhalten.
Die Anwendung von Heijunka führt zu einer stabilen Produktion und einer besseren Auslastung Ihrer Ressourcen.
Effizienzsteigerung durch Lean Management
Lean Management hilft dir, die Effizienz in der Produktion zu steigern. Es konzentriert sich auf die Minimierung von Verschwendung und die Verbesserung von Prozessen. Die Schwerpunkte liegen auf Just-in-Time-Produktion, der Optimierung des Materialflusses und dem kontinuierlichen Verbesserungsprozess (KVP).
Just-in-Time Produktion
Die Just-in-Time (JIT) Produktion ist ein wichtiger Ansatz im Lean Management. Hierbei wird Material genau dann geliefert, wenn es benötigt wird. Dadurch vermeidest du Überproduktion und Lagerkosten.
Durch JIT kannst du Ressourcen besser nutzen, da du nur das produzieren lässt, was aktuell nachgefragt wird. Dies führt nicht nur zu weniger Lagerbestand, sondern steigert auch die Flexibilität deiner Produktion.
Einigen Unternehmen gelingt es, ihre Produktionszeiten um bis zu 50 % zu verkürzen, wenn sie den JIT-Ansatz richtig umsetzen. Das bedeutet, dass du schneller auf Marktentwicklungen reagieren kannst.
Optimierung des Materialflusses
Ein effektiver Materialfluss ist entscheidend für die Effizienz deiner Produktion. Du solltest sicherstellen, dass Materialien und Produkte reibungslos durch den Produktionsprozess fließen.
Dazu gehört die Planung von Transportwegen und die Minimierung von Wartezeiten in der Produktion. Eine gute Logistik ist notwendig, um den Materialfluss zu verbessern.
Durch den Einsatz von visuellen Management-Tools kannst du Engpässe schnell erkennen und beheben. Beispielsweise können klare Markierungen und Schilder dir helfen, den Materialfluss zu steuern und Überlastungen zu vermeiden.
PDCA- und KVP-Zyklen
Der PDCA-Zyklus und KVP sind essentielle Werkzeuge im Lean Management. PDCA steht für Plan-Do-Check-Act und beschreibt einen kontinuierlichen Verbesserungsprozess.
Mit diesem Ansatz planst du Veränderungen, setzt sie um, überprüfst die Ergebnisse und nimmst Anpassungen vor. Dies fördert eine Kultur der ständigen Verbesserung.
KVP bedeutet, dass jeder Mitarbeiter aktiv in den Verbesserungsprozess einbezogen wird. Du kannst regelmäßige Meetings abhalten, um Ideen zu sammeln und Lösungen zu entwickeln, die die Effizienz weiter steigern.
Gemeinsam führen diese Methoden dazu, dass du häufige Probleme effizient identifizierst und löst, was langfristig die Produktivität erhöht.
Die Rolle der Mitarbeiter und Unternehmenskultur
Mitarbeiter spielen eine entscheidende Rolle in der Lean Production. Ihr Engagement und ihre Fähigkeiten sind wichtig, um Verschwendung zu minimieren und die Effizienz zu steigern.
Eine starke Unternehmenskultur fördert Teamarbeit. Wenn Mitarbeiter zusammenarbeiten, können sie Prozesse besser verstehen und optimieren. Offene Kommunikation ist dabei entscheidend.
Schulungen helfen, das Wissen über Lean-Methoden zu verbreiten. Gut ausgebildete Mitarbeiter können Probleme schneller erkennen und Lösungen finden. Regelmäßige Weiterbildung stärkt das Vertrauen in die Fähigkeiten des Teams.
Führungskräfte müssen eine unterstützende Rolle übernehmen. Sie sollten die Mitarbeiter in Entscheidungen einbeziehen und ein Umfeld schaffen, in dem Vorschläge willkommen sind. Partizipation fördert Motivation und Kreativität.
In der Lean Production geht es nicht nur um Prozesse, sondern auch um das Wohlbefinden der Mitarbeiter. Eine positive Unternehmenskultur führt zu höherer Zufriedenheit und weniger Fluktuation.
Zusammengefasst ist die Rolle der Mitarbeiter und der Unternehmenskultur für den Erfolg der Lean Production unverzichtbar. Engagierte Mitarbeiter und eine unterstützende Kultur sind Schlüssel zu einer effektiven Produktionsumgebung.
Lean Production Ergebnisse und Fallbeispiele
Lean Production führt zu bedeutenden Veränderungen in der Art und Weise, wie Unternehmen produzieren. Die folgenden Aspekte zeigen, wie Lean-Methoden die Produktqualität steigern, Durchlaufzeiten und Bestände reduzieren sowie die Kundenzufriedenheit erhöhen. Zudem werden praktische Fallstudien, insbesondere aus der Automobilindustrie, betrachtet.
Steigerung der Produktqualität
Durch die Implementierung von Lean Production steht die Produktqualität im Vordergrund. Methoden wie 5S (Sortieren, Setzen, Säubern, Standardisieren, Selbstdisziplin) sorgen für einen organisierten Arbeitsplatz, der Fehlerquellen minimiert.
Zusätzlich werden Qualitätskontrollen in jeder Produktionsphase durchgeführt. Dies führt dazu, dass Probleme frühzeitig erkannt werden.
Die konstante Verbesserung (Kaizen) fördert eine Kultur, in der Mitarbeiter Vorschläge zur Qualitätssicherung einbringen. Diese Maßnahmen helfen, nicht nur die Qualität des Endprodukts zu steigern, sondern auch die Zufriedenheit der Kunden zu erhöhen.
Reduktion von Durchlaufzeiten und Beständen
Ein zentrales Ziel von Lean Production ist die Reduktion der Durchlaufzeiten. Durch die Analyse von Arbeitsabläufen können Engpässe identifiziert und beseitigt werden.
Die Einführung der just-in-time-Produktion trägt dazu bei, dass Materialien nur bei Bedarf bereitgestellt werden. Dadurch werden hohe Lagerbestände vermieden.
Ein Beispiel sind Kanban-Systeme, die den Fluss von Materialien steuern und sicherstellen, dass nur die benötigten Mengen produziert werden. Das reduziert sowohl die Durchlaufzeiten als auch die Lagerkosten und steigert die Effizienz.
Erhöhung der Kundenzufriedenheit
Kundenzufriedenheit ist entscheidend für den Erfolg eines Unternehmens. Lean Production bietet verschiedene Ansätze, um Kundenbedürfnisse besser zu erfüllen. Engere Zusammenarbeit mit den Kunden hilft, deren Wünsche zu verstehen.
Durch die kürzeren Durchlaufzeiten können Produkte schneller geliefert werden.
Zusätzlich tragen verbesserte Produktqualitäten zur Steigerung der Kundenzufriedenheit bei. Wenn die Wünsche der Kunden erfüllt werden, stärkt das die Kundenbindung und fördert positive Bewertungen. Dies führt langfristig zu einem Wettbewerbsvorteil.
Fallstudien aus der Automobilindustrie
Die Automobilindustrie ist ein gutes Beispiel für erfolgreiche Lean-Implementierungen. Unternehmen wie Toyota revolutionierten das Produktionsmodell mit Lean-Methoden.
Ein konkretes Beispiel ist die Einführung des Toyota Production System (TPS). Dieses System fokussiert sich auf kontinuierliche Verbesserung und Verschlankung von Prozessen.
Zusätzlich haben viele Hersteller die Kaizen-Philosophie übernommen, um Mitarbeiter aktiv in den Verbesserungsprozess einzubeziehen. Die Ergebnisse sind deutlich: weniger Fehler, höhere Qualität und gesteigerte Effizienz.
Diese Fallstudien zeigen, wie Lean Production nicht nur die Prozesse optimiert, sondern auch die gesamte Branche voranbringt.
Häufig gestellte Fragen
In diesem Abschnitt werden grundlegende Fragen zur Lean Production behandelt. Dabei geht es um Definitionen, Vorteile, mögliche Nachteile, angewandte Methoden sowie die Hauptziele des Konzepts.
Was versteht man unter dem Begriff Lean Production?
Lean Production bezeichnet ein Konzept zur Prozessoptimierung in der Produktion. Es zielt darauf ab, Verschwendung zu minimieren und den Einsatz von Ressourcen wie Personal und Materialien zu optimieren.
Welche Vorteile bietet das Lean Production Konzept?
Das Lean Production Konzept bietet mehrere Vorteile. Dazu gehören eine höhere Effizienz, geringere Kosten und eine verbesserte Produktqualität. Unternehmen können zudem flexibler auf Kundenbedürfnisse reagieren.
Welche Nachteile können sich durch Lean Production ergeben?
Mögliche Nachteile der Lean Production sind Engpässe und höhere Drucksituationen für die Mitarbeiter. In manchen Fällen kann es auch zu einer Überoptimierung führen, die die Kreativität einschränkt.
Welche Methoden werden in der Lean Production angewandt?
In der Lean Production kommen verschiedene Methoden zum Einsatz. Dazu zählen die 5S-Methode, Kaizen und das Just-in-Time-System. Diese Methoden helfen dabei, Prozesse kontinuierlich zu verbessern.
Wie definiert sich das Lean-Konzept im Produktionskontext?
Im Produktionskontext bedeutet Lean, Ressourcen so effizient wie möglich zu nutzen. Es geht darum, alle Prozesse zu überprüfen und zu verbessern, um Abfälle zu reduzieren und den Wert für den Kunden zu steigern.
Welche Hauptziele verfolgt Lean Production?
Die Hauptziele von Lean Production sind die Maximierung der Effizienz und die Steigerung der Qualität. Unternehmen sollen durch die Reduzierung von Verschwendung und den optimalen Einsatz von Ressourcen wettbewerbsfähiger werden.
Lean Production ist ein modernes Konzept, das in der Industrie für mehr Effizienz und weniger Verschwendung sorgt. Indem Sie die Prinzipien der Lean Production anwenden, können Sie Ihre Produktionsprozesse optimieren und die Qualität Ihrer Produkte steigern. Dieses Konzept hat sich besonders in Unternehmen etabliert, die in einem wettbewerbsintensiven Umfeld agieren.
In diesem Artikel erhalten Sie einen klaren Überblick über die Grundlagen und Prinzipien von Lean Production. Sie werden lernen, wie Unternehmen diese Methoden erfolgreich umsetzen und welche Rolle die Mitarbeiter und die Unternehmenskultur dabei spielen. Zudem werden Ergebnisse und Fallbeispiele betrachtet, die die positiven Effekte von Lean Management aufzeigen.
Sehen Sie sich die verschiedenen Aspekte an, die Lean Production zu einem unverzichtbaren Teil der modernen Produktion machen. Entdecken Sie, wie Sie durch den gezielten Einsatz dieser Strategien Ihre Effizienz steigern und Verschwendung reduzieren können.
Key Takeaways
Lean Production verbessert die Effizienz in der Industrie.
Mitarbeiter und Unternehmenskultur sind entscheidend für den Erfolg.
Fallbeispiele zeigen die positiven Ergebnisse der Umsetzung.
Grundlagen und Prinzipien der Lean Production
Lean Production umfasst wichtige Prinzipien, die darauf abzielen, die Effizienz in der Produktion zu steigern. Die folgenden Aspekte konzentrieren sich auf das Minimieren von Verschwendung, die Anwendung von Pull- und Fluss-Prinzipien sowie die kontinuierliche Verbesserung.
Verschwendung minimieren - Die 7 Muda
Eines der Hauptziele von Lean Production ist es, Verschwendung, auch bekannt als Muda, zu reduzieren. Die 7 Muda sind:
Überproduktion: Mehr produzieren als nötig.
Warten: Verzögerungen in der Produktion.
Transport: Unnötige Bewegungen von Materialien.
Überbearbeitung: Zuviel Aufwand für einfache Aufgaben.
Bestände: Hohe Lagerbestände, die nicht benötigt werden.
Bewegung: Unnötige Bewegungen von Arbeitskräften.
Fehler: Mängel, die Nacharbeit erfordern.
Indem Sie diese Arten von Muda erkennen und beseitigen, verbessern Sie die Qualität und Effizienz Ihrer Produktionsprozesse.
Das Pull-Prinzip und Fluss-Prinzip
Das Pull-Prinzip ist eine zentrale Methode der Lean Production. Es bedeutet, dass Produktion nur dann erfolgt, wenn es eine Nachfrage gibt. Dies verhindert Überproduktion und sorgt für optimalen Ressourcenverbrauch.
Das Fluss-Prinzip zielt darauf ab, dass Materialien und Informationen ohne Unterbrechungen durch den Produktionsprozess fließen. Ziel ist es, Leerlaufzeiten zu minimieren und den gesamten Prozess effizient zu gestalten. Beide Prinzipien helfen, die Produktionszeit zu verringern und die Qualität zu steigern.
Kontinuierliche Verbesserung - Kaizen
Kaizen ist ein japanischer Begriff, der „kontinuierliche Verbesserung“ bedeutet. In der Lean Production ermutigt Kaizen alle Mitarbeiter, Vorschläge zur Verbesserung zu unterbreiten. Dies kann kleinen Veränderungen in der Arbeitsweise bis hin zu größeren Prozessanpassungen reichen.
Der Schlüssel zu Kaizen ist, regelmäßig kleine Schritte zur Optimierung zu unternehmen. So schaffen Sie eine Unternehmenskultur, in der ständige Verbesserungen standardmäßig integriert sind. Diese Herangehensweise trägt dazu bei, Fehler zu reduzieren und die Qualität zu verbessern.
Wertstromanalyse und -design
Die Wertstromanalyse ist ein Werkzeug zur Identifikation und Reduzierung von Verschwendung. Sie ermöglicht es Ihnen, den gesamten Prozess von der Idee bis zum Endprodukt zu visualisieren. Dabei können nicht wertschöpfende Schritte erkannt und eliminiert werden.
Das Wertstromdesign hingegen hilft, zukünftige Prozesse zu planen, die effizienter sind. Es zeigt, wie jeder Schritt im Produktionsprozess zur Wertschöpfung beiträgt und wo Optimierungen notwendig sind. So verbessern Sie sowohl Effizienz als auch Qualität der Produktionsabläufe.
Umsetzung der Lean Production im Betrieb
Die Umsetzung von Lean Production im Betrieb erfordert verschiedene spezifische Methoden. Diese Methoden helfen, Prozesse zu optimieren, Ressourcen effizient einzusetzen und Verschwendung zu minimieren. Wichtige Aspekte sind die Organisation am Arbeitsplatz, der Materialfluss und die Standardisierung von Abläufen.
5S-Methode
Die 5S-Methode steht für die fünf Schritte: Sortieren, Sitzen, Säubern, Standardisieren und Selbstdiziplin. Diese Schritte helfen, den Arbeitsplatz zu organisieren und beschleunigen die Produktionsprozesse.
Sortieren: Entfernen Sie unnötige Gegenstände, damit nur das bleibt, was wirklich benötigt wird.
Sitzen: Organisieren Sie das Arbeitsumfeld so, dass alles einfach erreichbar ist.
Säubern: Halten Sie den Arbeitsplatz sauber, um Fehler und Ausschuss zu vermeiden.
Standardisieren: Erstellen Sie klare Standards für alle Prozesse.
Selbstdiziplin: Fördern Sie eine Kultur, in der Mitarbeiter selbst für Ordnung sorgen.
Durch die Anwendung von 5S können Sie die Effizienz und Produktivität auf dem Arbeitsplatz erheblich steigern.
Kanban-System
Das Kanban-System ist ein visuelles Management-Tool, das den Materialfluss und die Produktion steuert. Mit Kanban können Sie den Bedarf an Materialien und Personal bedarfsorientiert planen.
Visualisierung: Nutzen Sie Tafeln oder Karten, um den Status von Aufträgen sichtbar zu machen.
Just-in-time: Stellen Sie sicher, dass Materialien und Produkte genau dann bereit sind, wenn sie benötigt werden, um Transportkosten und Lagerhaltung zu minimieren.
Flexibilität: Passen Sie die Produktion schnell an Veränderungen in der Nachfrage an, ohne viel Aufwand.
Diese Methode minimiert nicht nur Verschwendung, sondern verbessert auch die Kommunikation unter den Mitarbeitern.
Poka Yoke
Poka Yoke oder „Fehlervermeidung“ zielt darauf ab, menschliche Fehler im Produktionsprozess zu verhindern. Es handelt sich um einfache, oft mechanische Vorrichtungen oder Prozesse, die helfen, Fehler rechtzeitig zu erkennen.
Vorrichtungen: Verwenden Sie einfache Hilfsmittel, die sicherstellen, dass Teile nur auf eine Weise zusammengebaut werden können.
Prüfzellen: Integrieren Sie Prüfstationen, an denen Produkte auf Fehler überprüft werden.
Schulung: Schulen Sie Ihre Mitarbeiter, wie sie Poka Yoke-Prinzipien in ihren Aufgaben anwenden können.
Durch Poka Yoke reduzieren Sie den Ausschuss und verbessern die Qualität der Produkte.
Heijunka - Produktionsnivellierung
Heijunka bedeutet Produktionsnivellierung und beschäftigt sich mit der gleichmäßigen Verteilung von Arbeitslast und Produktionsvolumen. Dies hilft, Überlastung zu vermeiden.
Gleichmäßige Arbeit: Verteilen Sie die Produktionsaufträge über den Tag oder die Woche, um Spitzen und Täler zu vermeiden.
Bedarfsgerechte Planung: Planen Sie die Produktion basierend auf der tatsächlichen Nachfrage, um Überproduktion zu reduzieren.
Mitarbeiterförderung: Involvieren Sie Mitarbeiter in den Prozess, um Vorschläge zur Verbesserung der Arbeitsabläufe zu erhalten.
Die Anwendung von Heijunka führt zu einer stabilen Produktion und einer besseren Auslastung Ihrer Ressourcen.
Effizienzsteigerung durch Lean Management
Lean Management hilft dir, die Effizienz in der Produktion zu steigern. Es konzentriert sich auf die Minimierung von Verschwendung und die Verbesserung von Prozessen. Die Schwerpunkte liegen auf Just-in-Time-Produktion, der Optimierung des Materialflusses und dem kontinuierlichen Verbesserungsprozess (KVP).
Just-in-Time Produktion
Die Just-in-Time (JIT) Produktion ist ein wichtiger Ansatz im Lean Management. Hierbei wird Material genau dann geliefert, wenn es benötigt wird. Dadurch vermeidest du Überproduktion und Lagerkosten.
Durch JIT kannst du Ressourcen besser nutzen, da du nur das produzieren lässt, was aktuell nachgefragt wird. Dies führt nicht nur zu weniger Lagerbestand, sondern steigert auch die Flexibilität deiner Produktion.
Einigen Unternehmen gelingt es, ihre Produktionszeiten um bis zu 50 % zu verkürzen, wenn sie den JIT-Ansatz richtig umsetzen. Das bedeutet, dass du schneller auf Marktentwicklungen reagieren kannst.
Optimierung des Materialflusses
Ein effektiver Materialfluss ist entscheidend für die Effizienz deiner Produktion. Du solltest sicherstellen, dass Materialien und Produkte reibungslos durch den Produktionsprozess fließen.
Dazu gehört die Planung von Transportwegen und die Minimierung von Wartezeiten in der Produktion. Eine gute Logistik ist notwendig, um den Materialfluss zu verbessern.
Durch den Einsatz von visuellen Management-Tools kannst du Engpässe schnell erkennen und beheben. Beispielsweise können klare Markierungen und Schilder dir helfen, den Materialfluss zu steuern und Überlastungen zu vermeiden.
PDCA- und KVP-Zyklen
Der PDCA-Zyklus und KVP sind essentielle Werkzeuge im Lean Management. PDCA steht für Plan-Do-Check-Act und beschreibt einen kontinuierlichen Verbesserungsprozess.
Mit diesem Ansatz planst du Veränderungen, setzt sie um, überprüfst die Ergebnisse und nimmst Anpassungen vor. Dies fördert eine Kultur der ständigen Verbesserung.
KVP bedeutet, dass jeder Mitarbeiter aktiv in den Verbesserungsprozess einbezogen wird. Du kannst regelmäßige Meetings abhalten, um Ideen zu sammeln und Lösungen zu entwickeln, die die Effizienz weiter steigern.
Gemeinsam führen diese Methoden dazu, dass du häufige Probleme effizient identifizierst und löst, was langfristig die Produktivität erhöht.
Die Rolle der Mitarbeiter und Unternehmenskultur
Mitarbeiter spielen eine entscheidende Rolle in der Lean Production. Ihr Engagement und ihre Fähigkeiten sind wichtig, um Verschwendung zu minimieren und die Effizienz zu steigern.
Eine starke Unternehmenskultur fördert Teamarbeit. Wenn Mitarbeiter zusammenarbeiten, können sie Prozesse besser verstehen und optimieren. Offene Kommunikation ist dabei entscheidend.
Schulungen helfen, das Wissen über Lean-Methoden zu verbreiten. Gut ausgebildete Mitarbeiter können Probleme schneller erkennen und Lösungen finden. Regelmäßige Weiterbildung stärkt das Vertrauen in die Fähigkeiten des Teams.
Führungskräfte müssen eine unterstützende Rolle übernehmen. Sie sollten die Mitarbeiter in Entscheidungen einbeziehen und ein Umfeld schaffen, in dem Vorschläge willkommen sind. Partizipation fördert Motivation und Kreativität.
In der Lean Production geht es nicht nur um Prozesse, sondern auch um das Wohlbefinden der Mitarbeiter. Eine positive Unternehmenskultur führt zu höherer Zufriedenheit und weniger Fluktuation.
Zusammengefasst ist die Rolle der Mitarbeiter und der Unternehmenskultur für den Erfolg der Lean Production unverzichtbar. Engagierte Mitarbeiter und eine unterstützende Kultur sind Schlüssel zu einer effektiven Produktionsumgebung.
Lean Production Ergebnisse und Fallbeispiele
Lean Production führt zu bedeutenden Veränderungen in der Art und Weise, wie Unternehmen produzieren. Die folgenden Aspekte zeigen, wie Lean-Methoden die Produktqualität steigern, Durchlaufzeiten und Bestände reduzieren sowie die Kundenzufriedenheit erhöhen. Zudem werden praktische Fallstudien, insbesondere aus der Automobilindustrie, betrachtet.
Steigerung der Produktqualität
Durch die Implementierung von Lean Production steht die Produktqualität im Vordergrund. Methoden wie 5S (Sortieren, Setzen, Säubern, Standardisieren, Selbstdisziplin) sorgen für einen organisierten Arbeitsplatz, der Fehlerquellen minimiert.
Zusätzlich werden Qualitätskontrollen in jeder Produktionsphase durchgeführt. Dies führt dazu, dass Probleme frühzeitig erkannt werden.
Die konstante Verbesserung (Kaizen) fördert eine Kultur, in der Mitarbeiter Vorschläge zur Qualitätssicherung einbringen. Diese Maßnahmen helfen, nicht nur die Qualität des Endprodukts zu steigern, sondern auch die Zufriedenheit der Kunden zu erhöhen.
Reduktion von Durchlaufzeiten und Beständen
Ein zentrales Ziel von Lean Production ist die Reduktion der Durchlaufzeiten. Durch die Analyse von Arbeitsabläufen können Engpässe identifiziert und beseitigt werden.
Die Einführung der just-in-time-Produktion trägt dazu bei, dass Materialien nur bei Bedarf bereitgestellt werden. Dadurch werden hohe Lagerbestände vermieden.
Ein Beispiel sind Kanban-Systeme, die den Fluss von Materialien steuern und sicherstellen, dass nur die benötigten Mengen produziert werden. Das reduziert sowohl die Durchlaufzeiten als auch die Lagerkosten und steigert die Effizienz.
Erhöhung der Kundenzufriedenheit
Kundenzufriedenheit ist entscheidend für den Erfolg eines Unternehmens. Lean Production bietet verschiedene Ansätze, um Kundenbedürfnisse besser zu erfüllen. Engere Zusammenarbeit mit den Kunden hilft, deren Wünsche zu verstehen.
Durch die kürzeren Durchlaufzeiten können Produkte schneller geliefert werden.
Zusätzlich tragen verbesserte Produktqualitäten zur Steigerung der Kundenzufriedenheit bei. Wenn die Wünsche der Kunden erfüllt werden, stärkt das die Kundenbindung und fördert positive Bewertungen. Dies führt langfristig zu einem Wettbewerbsvorteil.
Fallstudien aus der Automobilindustrie
Die Automobilindustrie ist ein gutes Beispiel für erfolgreiche Lean-Implementierungen. Unternehmen wie Toyota revolutionierten das Produktionsmodell mit Lean-Methoden.
Ein konkretes Beispiel ist die Einführung des Toyota Production System (TPS). Dieses System fokussiert sich auf kontinuierliche Verbesserung und Verschlankung von Prozessen.
Zusätzlich haben viele Hersteller die Kaizen-Philosophie übernommen, um Mitarbeiter aktiv in den Verbesserungsprozess einzubeziehen. Die Ergebnisse sind deutlich: weniger Fehler, höhere Qualität und gesteigerte Effizienz.
Diese Fallstudien zeigen, wie Lean Production nicht nur die Prozesse optimiert, sondern auch die gesamte Branche voranbringt.
Häufig gestellte Fragen
In diesem Abschnitt werden grundlegende Fragen zur Lean Production behandelt. Dabei geht es um Definitionen, Vorteile, mögliche Nachteile, angewandte Methoden sowie die Hauptziele des Konzepts.
Was versteht man unter dem Begriff Lean Production?
Lean Production bezeichnet ein Konzept zur Prozessoptimierung in der Produktion. Es zielt darauf ab, Verschwendung zu minimieren und den Einsatz von Ressourcen wie Personal und Materialien zu optimieren.
Welche Vorteile bietet das Lean Production Konzept?
Das Lean Production Konzept bietet mehrere Vorteile. Dazu gehören eine höhere Effizienz, geringere Kosten und eine verbesserte Produktqualität. Unternehmen können zudem flexibler auf Kundenbedürfnisse reagieren.
Welche Nachteile können sich durch Lean Production ergeben?
Mögliche Nachteile der Lean Production sind Engpässe und höhere Drucksituationen für die Mitarbeiter. In manchen Fällen kann es auch zu einer Überoptimierung führen, die die Kreativität einschränkt.
Welche Methoden werden in der Lean Production angewandt?
In der Lean Production kommen verschiedene Methoden zum Einsatz. Dazu zählen die 5S-Methode, Kaizen und das Just-in-Time-System. Diese Methoden helfen dabei, Prozesse kontinuierlich zu verbessern.
Wie definiert sich das Lean-Konzept im Produktionskontext?
Im Produktionskontext bedeutet Lean, Ressourcen so effizient wie möglich zu nutzen. Es geht darum, alle Prozesse zu überprüfen und zu verbessern, um Abfälle zu reduzieren und den Wert für den Kunden zu steigern.
Welche Hauptziele verfolgt Lean Production?
Die Hauptziele von Lean Production sind die Maximierung der Effizienz und die Steigerung der Qualität. Unternehmen sollen durch die Reduzierung von Verschwendung und den optimalen Einsatz von Ressourcen wettbewerbsfähiger werden.

am Montag, 2. September 2024